There are several processes that occurs in the wholesale distribution and supply chain management process before goods are shipped to the final customer. One of such processes is warehouse inventory management.
Staying on top of your warehouse inbound process flow is necessary to achieve efficient business systems. From inventory management and inventory control to adopting smart warehouse technology and using warehouse management systems, there is a lot that goes into running a warehouse.
As a b2b eCommerce business, fulfilling orders accurately and efficiently is crucial to keeping your customers happy. One way to achieve this goal is by implementing a comprehensive warehouse order checklist.
Key Takeaway: A well-designed checklist can help streamline the order fulfillment process, reducing the risk of errors, and increasing productivity. In this blog, we'll be exploring the 5 best practices for warehouse omnichannel order fulfillment and how a thorough warehouse order checklist can support these efforts.
Whether you're just starting out or looking to improve existing processes, these tips will help ensure your warehouse is running smoothly and your customers are receiving their orders in a timely manner.
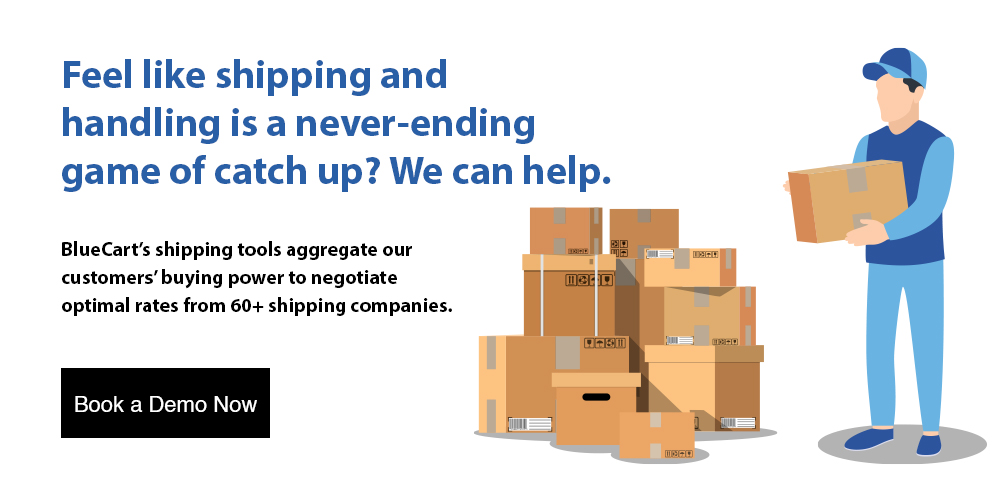
What is a Warehouse Order Checklist?
A warehouse order checklist is a step-by-step guide used to ensure that the process of picking, packing, and shipping and handling orders from a warehouse is done accurately and efficiently. It outlines the various tasks involved in fulfilling an order, such as verifying inventory levels, picking and packaging items, and checking the shipping address, among others.
The use of a warehouse order checklist helps to minimize errors and ensures that all necessary steps are taken to fulfill an order correctly. It also provides a reference for future order fulfillment processes, ensuring consistency and reliability in the warehouse operations.
Let’s look at an instance of how a coffee beans wholesale business will use a warehouse order checklist to ensure the smooth and accurate fulfillment of orders from their warehouse:
- Order Verification: The first step in the process is to verify the order details, including the type of coffee beans, quantity, and shipping address.
- Inventory Check: The next step is to check the inventory levels to ensure that the required coffee beans are available.
- Picking and Packaging: The selected coffee beans are picked and packaged securely to ensure they reach the customer in good condition.
- Shipping: The packaged coffee beans are then shipped to the customer, and the shipping address is double-checked to ensure it is correct.
- Quality Control: The final step is to inspect the packaged coffee beans for any damages and to verify that the correct type and quantity of beans were shipped.
By following a warehouse order checklist, the wholesale coffee bean business can ensure that orders are fulfilled accurately and efficiently. Thus, reducing the risk of errors and improving customer satisfaction.
Complete Warehouse Order Checklist
Here’s how your warehouse order checklist should look like:
#1. Receive Order: Verify the order and confirm its accuracy.
#2. Pick Order: Retrieve the items from the shelves and place them in a designated area.
#3. Pack Order: Package the items securely and label them with the customer's address and order details.
#4. Quality Control: Inspect the items to ensure they are in good condition and match the order specifications.
#5. Ship Order: Choose the appropriate shipping method, generate shipping label and dispatch the order.
#6. Update Inventory: Decrease the quantity of the items in the inventory management system.
#7. Customer Communication: Notify the customer that the order has been shipped and provide tracking information.
#8. Document Process: Keep record of the order fulfillment process for reference and future analysis.
#9. Review Performance: Regularly evaluate and improve the order fulfillment process to maximize efficiency and customer satisfaction.
Note: This is a general warehouse order checklist, and specific steps may vary depending on your company's processes and systems.
Warehouse Order Checklist: 5 Best Practices for Warehouse Fulfillment
Running an efficient warehouse distribution operation is key to providing your customers with a seamless offline and online ordering experience. In order to achieve this, it’s essential to have a thorough warehouse order checklist in place.
Here are five best practices for ensuring a smooth and effective warehouse fulfillment process:
- Accurate Inventory Management: Maintaining an up-to-date and accurate inventory is crucial for ensuring that orders are fulfilled on time and the warehousing process is smooth. This includes regularly monitoring inventory levels, identifying and resolving discrepancies, and implementing real-time updates to ensure inventory accuracy.
- Streamlined Pick, Pack and Ship Process: A well-defined pick, pack and ship process can help to minimize errors and reduce lead time. This includes having a clear and easy-to-follow system for picking items, packing them securely and labeling them correctly with warehouse label software, and then shipping them out in a timely manner.
- Effective Communication: Good communication is vital for ensuring a smooth and efficient warehouse operation. This includes regular communication with customers and other departments, as well as clear and concise instructions for warehouse staff.
- Proper Training: Providing your warehouse staff with proper training and resources is essential for ensuring that orders are fulfilled accurately and efficiently. This includes regular training on new processes and technologies, as well as providing access to the tools and resources needed to do their job effectively.
- Use of Technology: Technology can play a crucial role in streamlining and optimizing the warehouse fulfillment process. This includes the use of warehouse management systems, barcode scanning and labeling systems, and real-time data analytics to monitor and improve the process.
By following these best practices, you can ensure that your warehouse operation is running smoothly and effectively, resulting in a seamless and satisfying customer experience.
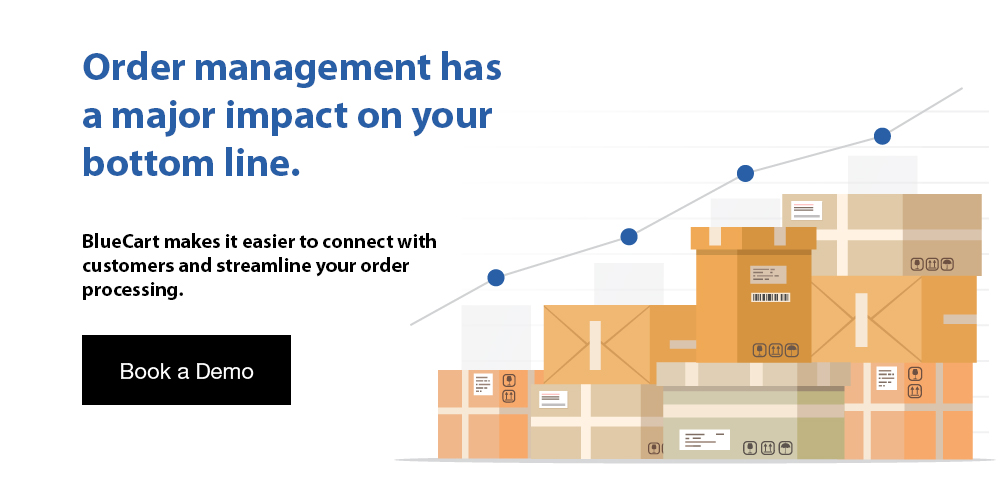
7 Benefits of a Warehouse Order Picking Checklist
So, why should you use a warehouse order checklist to streamline your warehouse operations? Let’s find out.
- Accuracy: A warehouse order picking checklist helps to reduce the risk of errors in the order fulfillment process, ensuring that orders are picked, packaged, and shipped accurately.
- Consistency: By following a standardized process, a warehouse order checklist ensures consistency in the fulfillment of orders, improving the reliability of the warehouse operations.
- Efficiency: The use of a warehouse order picking checklist helps to streamline the order fulfillment process, reducing the time and resources required to fulfill each order.
- Improved Productivity: By minimizing errors and reducing the time required to fulfill orders, a warehouse order checklist can help to improve the productivity of the warehouse operations.
- Better Customer Experience: By ensuring that orders are fulfilled accurately and efficiently, a warehouse receiving checklist helps to improve the omnichannel customer experience and reduce the risk of customer complaints and returns.
- Record Keeping: A warehouse order checklist provides a record of the steps taken in the order fulfillment process, allowing the business to track its performance and identify areas for improvement.
- Training and Onboarding: A warehouse order checklist can serve as a warehouse management guide and be used as a training tool for new employees, helping them to quickly understand the order fulfillment process and get up to speed with the operations of the warehouse.
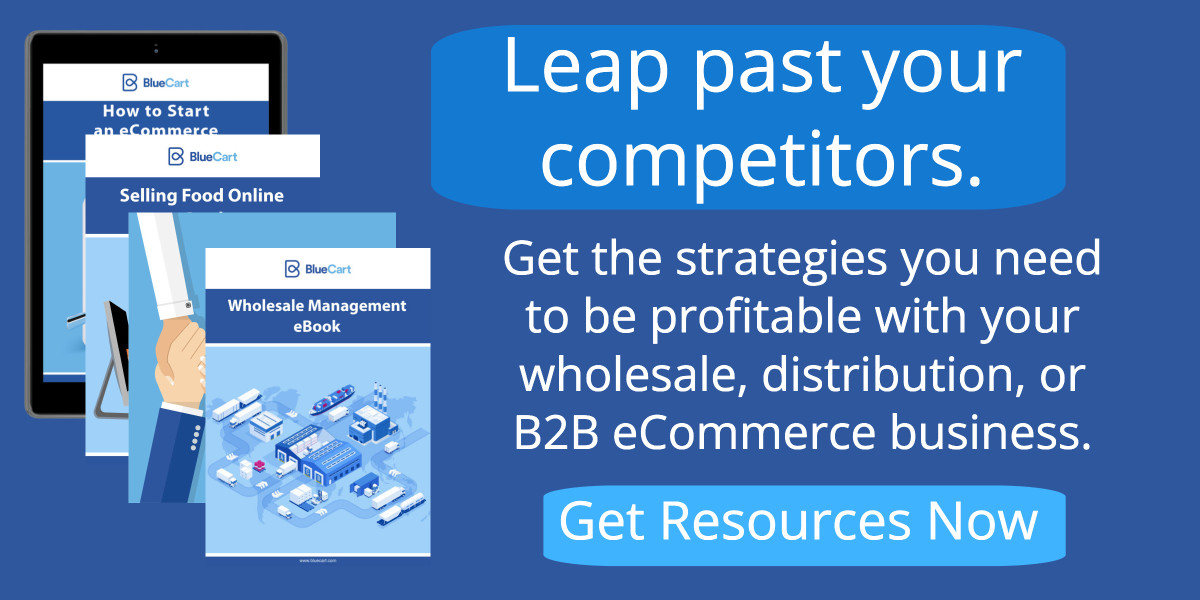
Frequently Asked Questions About Warehouse Order Checklist
Here are some frequently asked questions about warehouse order checklist.
What is Warehouse Checklist?
A warehouse checklist is a document that outlines the steps and processes involved in fulfilling various warehouse operations with the ultimate goal of achieving seamless order fulfillment. It includes tasks such as receiving an order, picking items, packing and labeling, shipping, updating inventory, communicating with customers, documenting the process, and reviewing performance.
What are 7 Guidelines for Efficient Receiving Procedures?
Seven guidelines for efficient receiving procedures are:
- Accurate Documentation: Ensure that all receiving documents are complete, accurate and legible.
- Verification of Shipments: Verify that the items received match the purchase order or packing slip.
- Inspections for Damage: Inspect all items for damage or discrepancies before accepting them.
- Timely Receiving: Schedule receiving activities to minimize downtime and ensure timely processing of shipments.
- Physical Counts: Conduct physical counts of received items to verify accuracy and ensure inventory accuracy.
- Proper Storage: Store received items in designated areas and follow proper storage guidelines.
- Record Keeping: Maintain accurate and up-to-date records of all receiving activities, including discrepancies and damages.
What is the 6S Checklist for Warehouse?
The 6S checklist for warehouse is a methodology used to organize and optimize warehouse operations and it stands for the following six steps:
- Sort: Remove items that are not needed or are taking up valuable space.
- Set in Order: Arrange items in a logical and organized manner to minimize the time and effort required to find and retrieve them.
- Shine: Clean the warehouse to ensure that it is safe and hygienic, and to make it easier to identify any potential problems.
- Standardize: Establish clear processes and procedures to ensure consistency and efficiency.
- Sustain: Maintain the improvements made during the 6S process by continuously monitoring and improving processes.
- Safety: Make safety a priority by identifying and addressing potential hazards and following established safety protocols.
The Bottomline is…
Implementing a comprehensive warehouse order checklist and following best practices for receiving procedures can play a crucial role in ensuring that your warehouse operations are efficient and effective. By adhering to these guidelines, you can streamline your order fulfillment process, reduce the risk of errors, and improve the overall customer experience.
So, if you haven't already, consider incorporating these strategies into your warehouse operations today and reap the benefits of a well-run and efficient warehouse.