Inventory is a crucial part of running a business, especially if you’re in the retail or eCommerce sector. Using proper inventory management techniques will help you make the right decisions for your business. These techniques can also help you avoid phantom inventory.
Most businesses will plan and track limited-time promotions, product merchandising, and store layouts. However, these can become difficult to track if you don’t know the true number of inventory on hand.
If your business is dealing with phantom inventory, it may lead to unsatisfied customers, loss of sales, and inaccurate data. This blog post covers the phantom inventory meaning and four ways to avoid it.
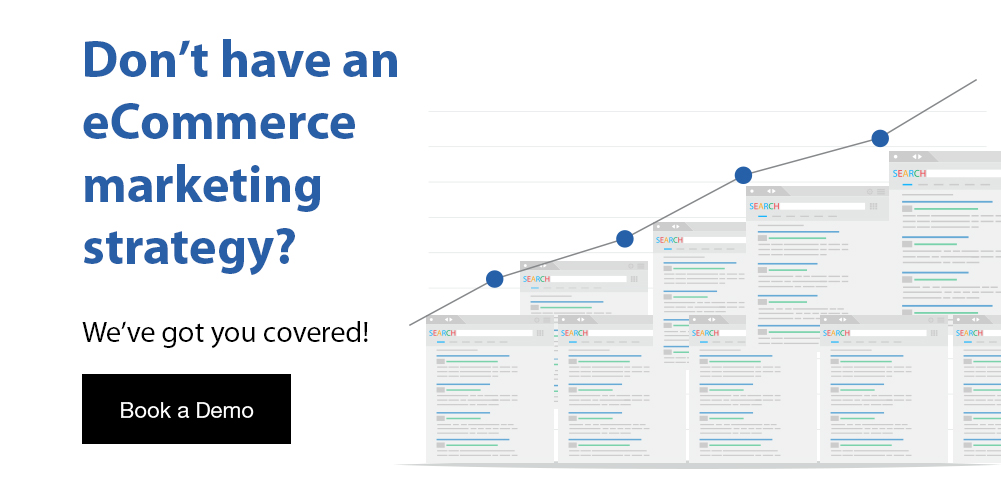
Phantom Inventory Meaning
The meaning of phantom inventory refers to inventory that doesn’t physically exist for the business to utilize. In other words, it’s inventory your data system, such as your inventory report, says you have available. However, when you physically check, you don’t have the inventory in stock.
Phantom inventory is often a result of inventory shrinkage, missing or stolen inventory. This can lead to business loss, a decrease in profit margins, and a potential loss in customers.
In many cases, phantom inventory occurs due to misplacement, breakage, theft, and data entry errors. It can cause discrepancies between inventory records and real inventory. If the phantom inventory isn’t properly addressed, it can negatively impact the business when it comes to accounting adjustments and restatements.
Key Takeaway: If unaddressed, phantom inventory can end up becoming costly and detrimental to your business. However, integrating best practices will allow you to identify and prevent phantom inventory problems before they result in lost revenue.
Causes of Phantom Inventory
It’s important to catch issues regarding phantom inventory before they cause long-term problems. In order to do this, you need to understand the causes of phantom inventory.
Common causes of phantom inventory include:
Shrinkage
The loss of inventory due to employee theft, shoplifting, and fraud is known as shrinkage.
Recording Incorrect Sales
Recording sales is simple with a POS system, this includes a restaurant POS if you’re in the restaurant industry. However, there is still a chance for error. This is possible if you incorrectly scan a product at checkout. As a result, it won’t be accounted for in real-time inventory.
Such errors commonly occur as a result of an in-store sales error. For example, if your company sells two items of the same model but different colors, and you choose to scan one of the items twice due to the items being the same price. This will causes skew stock levels for both colors of the product and lead to phantom inventory for the color that wasn’t scanned.
These reasons are why each individual product will have a unique SKU number or UPC code. The numbers represent the details of the product, including the size, color, and similar details.
Lack of Inventory Audits
Small cases of phantom inventory may seem like a minimal problem for your business. However, over time, they can become large problems, especially if you don’t perform routine inventory audits to catch these minor discrepancies.
It’s recommended for businesses to perform physical inventory counts at least once a year. Smaller batches of inventory should be checked using cycle counting methods. These smaller batches include your best-selling products, such as high demand products, your stock that contributes the most to revenue, and products from specific vendors.
Receiving Errors
Manual data entries are risky as they can often lead to human errors. This is especially common when receiving inventory. For example, employees may record more units than they actually receive or forget to account for breakage. This often happens when taking inventory using physical methods compared to electronic methods.
Misplaced Inventory
A disorganized stockroom or warehouse may cause more misplaced inventory than you expect. That’s why proper warehousing and inventory storage is important. This will also help with holiday inventory management and prevent overselling.
Misplaced inventory means that you have the inventory, but it’s hard to locate. A way this can happen is if customers move your products to different parts of the store. This includes after they try it on or change their mind about purchasing it. You may also misplace inventory after you receive a return.
As a business owner or manager, you can avoid misplacing inventory by regularly tidying up your sales floor each day. You may also consider having a system for your employees to follow when it comes to organizing your stockroom.
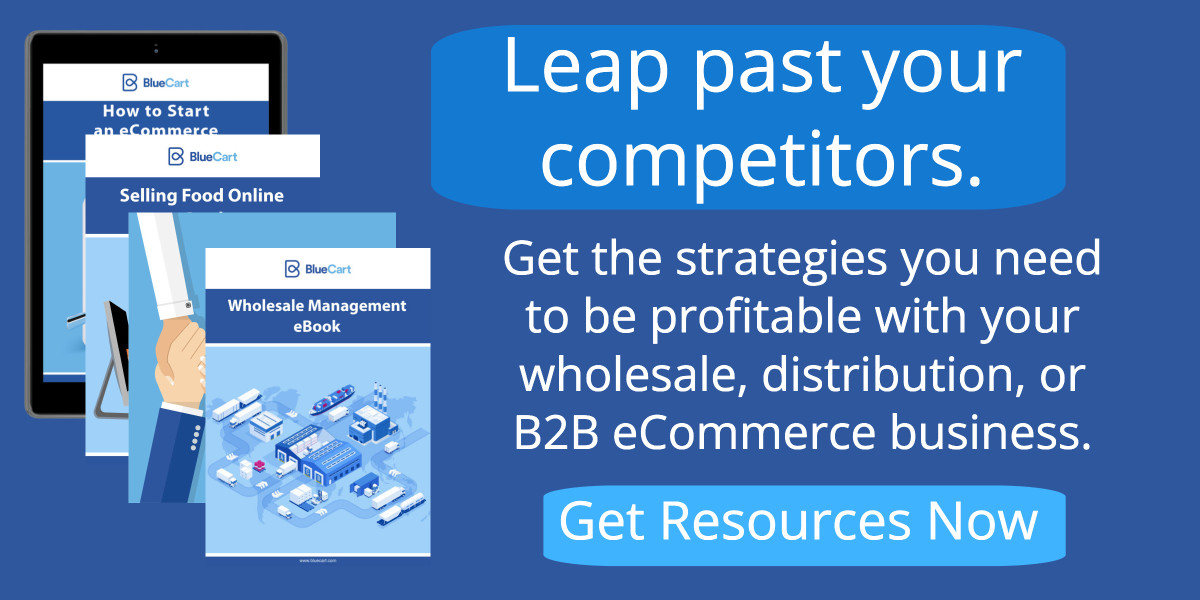
4 Ways To Avoid Phantom Inventory
It’s not always easy to identify the phantom inventory in your business. This is often because the inventory numbers increase the chance of having phantom inventory. However, there are multiple ways to avoid phantom inventory.
Four ways to avoid phantom inventory include:
1. Inventory Cycle Counts
The process of performing inventory cycle counts is similar to the audit process. In other words, it’s a perpetual inventory count. For this process, accuracy is crucial.
Cycle counts are useful for identifying the source of the discrepancy and monitoring the effectiveness of each step taken to eliminate the discrepancy. During this process, businesses will compare the previous year's statistics to the current year’s data.
No inventory change will result in the cycle being similar to the previous year. If there is a change, you will have to pay attention to the factors that influenced the numbers.
2. Utilize Automated Software
Businesses can use automated software to eliminate phantom inventory. It helps automate the process and helps with tagging inventory to make it a simple process. Common automated software includes automated billing software and dropshipping automation software.
Automated inventory software works using real-time and unique identification numbers that the system stores once tags are scanned. Systems automatically retrieve information once a product is purchased or sold and allows inventory levels to update. This can decrease the chance of phantom inventory occurring.
3. Routine Audits
Audits are time-consuming and long processes, especially when you have a lot of inventory on hand. However, they provide businesses with a true picture of the inventory they have in their warehouse.
Once you conduct the audit, you can compare data records to identify if you have phantom inventory or not. It’s ideal to perform inventory audits on a routine basis to get the best results.
4. Tagging Inventory
An effective way to avoid phantom inventory is by tagging inventory. This will save you time, so you don’t have to look for specific inventory since the tags will make it easy to find.
This process can also help prevent inventory misplacement and theft. You will also be aware of where your inventory is. Inventory tracking is also possible using radio-frequency identification methods and quick response codes (QR code).
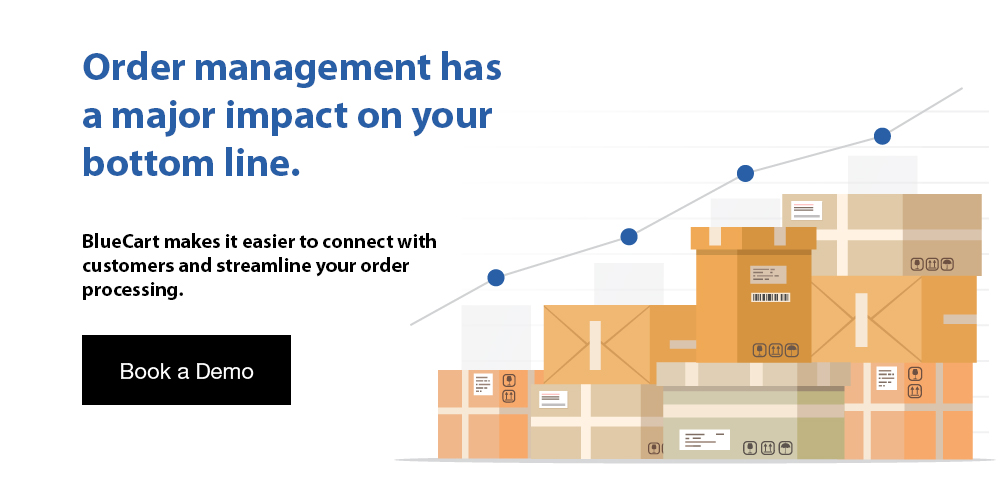
Frequently Asked Questions About Phantom Inventory
There are different ways to find out if your business has phantom inventory. However, the best way to do so is through the use of automated software, including inventory management software. This includes restaurant inventory management software.
To better understand phantom inventory, read the following commonly asked questions:
How Do I Fix Phantom Inventory?
To fix phantom inventory, you can perform manual inventory resets. This means recounting each product and performing audits on a regular basis. It’s also important to keep track of your inventory metrics, such as days inventory outstanding and weighted average cost.
What Is Phantom Stockout?
Phantom stockout refers to a stockout phenomenon in retail that is often caused by unobserved inventory shrinkage. It’s possible to correct a conventional stockout with inventory replenishment; however, phantom stockouts require human inspection.
What Are the Main Reasons That Phantom Inventory Exists?
The main reason that phantom inventory exists is having incorrect data regarding the sales and purchases of your inventory. Another common reason is inventory misplacement and theft. To avoid phantom inventory, businesses may use a centralized inventory method and an inventory scanner.