Did you happen upon this article because you were looking for information regarding bicycle inventory? Well, you're in the wrong place.
Stick around anyway, as cycle stock inventory is one of the most important inventory management techniques. It is the portion of your stock that will make or break your business whether you use the B2B business model or use a direct to consumer business model. So, it's important to be able to track and understand cycle inventory. It’s one of the most integral parts of a business operation.
We'll walk you through the basics of cycle inventory, the average time for cycling, and give you tips on how to manage yours. We also provide a cycle inventory formula to make it easy to track cycle inventory. Keep reading to learn everything you need to know.
.jpg)
Cycle Inventory Definition
Cycle inventory, or cycle stock inventory, is the portion of inventory that a seller cycles through to fulfill regular sales orders. It represents a part of a business's standing inventory.
Cycle inventory is used and replaced by new items, or turned over. It is similar to tracking your sell through rate with a few added steps. There are a few differences between cycle stock in B2B vs. B2C businesses, so make sure you know what works for yours.
Cycle Inventory In Operation Management
Cycle inventory in operation management can make or break warehousing operations. Maintaining proper inventory control is a part of every operations manager's job. Inventory cycle count is an important way to regulate stock and ensure your operations remain efficient.
If inventory comes in or goes out at an unacceptable pace, operations can become stalled or overwhelmed. That's why many depend on ABC inventory analysis.
Supply Chain Cycle Inventory
Cycle inventory in supply chain management affects businesses in the chain as it directly impacts the goods they have on-hand and their ability to fulfill orders. Supply chain cycle inventory issues are caused by a number of factors:
- Demand. If demand rises or falls, the amount of inventory moving in the supply chain is directly impacted. Understanding demand changes can allow a business to react appropriately to increase sales and limit costs. Improper order management process based on incorrect data can cause a backlog that can quickly lead to losses.
- Order lead time. The time it takes between an order being placed and the product arriving (see lead time definition) can cause issues with cycle inventory. It is one of the biggest causes of a backorder in inventory management. Investing in route optimization software may help mitigate these issues.
- Storage costs. The cost of storing inventory rises and falls based on inventory levels and the cycle length.
Inventory and Warehousing Cycle
Warehouse management and the inventory cycle are directly related. The flow of goods in and out is a warehouse manager's primary duty. This means that understanding your business's inventory cycle time is paramount.
It will allow you to limit warehouse costs while maximizing the amount of sellable inventory. That’s one of the reasons it’s important to understand inventory cycle time.
What Is Inventory Cycle Time?
Inventory cycle time is the frequency of inventory replacement. That is, the amount of time taken from the start to finish of inventory use.
In retail, this is the time between a product arriving in your warehouse and it being sold. In manufacturing, it is the time taken from beginning production to the end of manufacturing activities. In simpler terms, it is the amount of time it takes raw materials inventory to become finished goods.
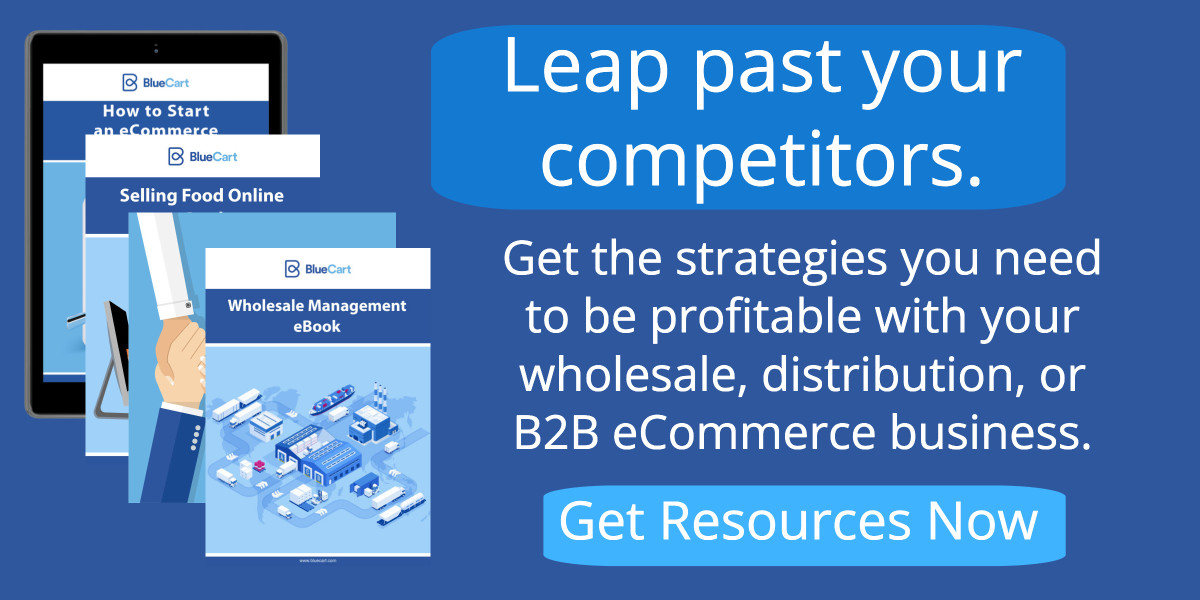
Cycle Count Inventory Definition
Cycle count is a part of inventory auditing where only a small portion of inventory is counted on a given day. This is in contrast to a full audit where every item in the inventory is counted. Cycle count is a sampling technique used to see how accurate inventory records are.
What Does Cycle Count Mean In Inventory Management?
In terms of the inventory management process, cycle count is taking sample inventories to cross-check inventory records. Though not a totally accurate measure for the full scope of inventory, cycle counts highlight any discrepancies in product counts. This alerts you to potential inventory issues and signals that it may be time to take a full inventory.
Physical Inventory vs Cycle Counting
.jpg)
Physical inventory is taking a manual count of every product in your inventory, while cycle counting is a much smaller count of inventory. Cycle counting has many benefits over traditional physical counts of inventory. Here are four main benefits of cycle counting:
- Saves time and labor. Since cycle counting deals with far fewer products, it takes less time to perform an inventory audit and doesn't require many staff members.
- Reduces inventory variance more quickly. If there are issues with shrinkage and variance, a physical inventory wouldn't discover it for at least a few weeks. Cycle counting can uncover these issues within a few inventory days.
- Doesn't require business shutdown. Full inventory count means all employees must spend their time taking inventory and no other business can be down. Cycle counting can be done during regular hours without interfering with operations.
- Happens more often and on specific products. If there is a particular good that you are concerned about, you can easily cycle count it on a regular basis limiting risk.
Cycle Inventory Management Tips
Cycle inventory management is important to ensure the correct products are being tracked and that no time or energy is wasted.
Here are the best ways to ensure you're doing it correctly:
- Prioritize important products. Don't waste time cycle counting rarely-used or sold products. Pick high demand products and have them regularly counted to avoid any surprises. For example, if you participate in kitting, you would choose to track the kits themselves, not the individual parts.
- Do counts as often as possible. Since cycling counting takes such little time and effort, do it as often as possible. This will allow you to stay on top of your inventory without having to shut down for a full physical inventory.
- Have a plan. Don't just count at random. Think through when, where, and how you want to count your goods so you don't waste valuable time or money.
- Budget appropriately. Though cycle counting costs far less than physical inventory, costs still rise when your business grows. Set aside the right budget to ensure the counts are done regularly.
- Assign counting to one or two employees. You don't have time for inventory counting and you don't want to train everyone to do it and take them off their other tasks. Pick one or two employees who regularly participate in cycle counting and you'll always have the data you need to succeed.
What Is the Primary Lever to Reduce Cycle Inventory?
The primary lever to reduce cycle inventory is to reduce lot sizes. Smaller lots require less work and don't allow for as many new goods to arrive before selling the current goods.
Too much safety stock is the primary cause of cycle inventory length being too long. It’s vital to carry just the right amount of safety stock for your business to avoid any issues with your cycle inventory length.
Managing Inventory for Short Life Cycle Products
Short life cycle products need to be tracked more often to ensure reordering is done in a timely manner. It’s important to know the reorder point of your products. Cycle counts are the best way to manage short life cycle products as they can regularly be monitored and any shift in demand can be reacted to more quickly.
Sales trends from these cycle counts also give insight into inventory level shifts and can be used to market the goods and optimize profits. This is particularly important if you receive or send inventory via bulk shipping.
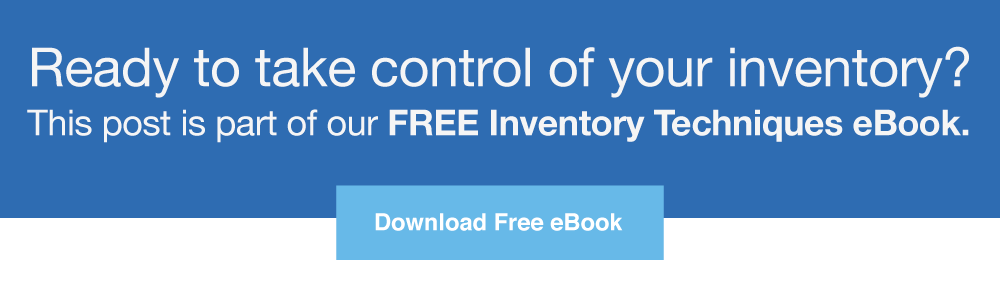
Inventory Accuracy Cycle Counting
Cycle count accuracy measures the percentage of cycle counts that did not require any adjustments. This means that the cycle counts matched the numbers from your inventory tracking.
The higher this number is, the less variance and shrinkage in your inventory. If there are adjustments made after cycle counts, you need to review your inventory methodology and discover where the issues are originating.
You should aim to have a 100% cycle count accuracy, but there is usually a small amount of inaccuracies for any business. Find a number you consider reasonable for your business and aim to stay at or above it. It's an important inventory KPI to control.
Average Cycle Inventory Formula
To find your average cycle inventory, you just need to use a simple formula. It will help you streamline the operations of your business and avoid any issues with cycle inventory.
Here is the formula you'll need:
Average Cycle Inventory = Lot Size / 2
The Cycle of Life
The inventory cycle has a direct impact on your business's ability to fulfill orders and make a profit. Tracking this cycle can keep you ahead of any issues that may arise and cycle counting is the best way to do this.
If you consistently find that your inventory count is too low, you may want to look into just in time inventory so you are regularly restocked. Or use consignment inventory or dropshipping to skip this process altogether. You can usually find suppliers who support these models on an online marketplace.
Frequently Asked Questions About Inventory Cycle Count
Mastering inventory cycle count should be on any warehouse manager resume or business owner’s radar. If you want to learn more of the ins and outs of cycle counting, check out the frequently asked questions below:
What Is the Cycle Count Inventory Definition?
Cycle count refers to the part of a company's inventory auditing process that includes a small portion of inventory that is counted on a certain day. The cycle rate definition differs from a full audit where the entire inventory is counted. Cycle count is a technique that is used to determine how accurate the inventory records are.
What Is the Supply Chain Cycle?
The supply chain cycle refers to the steps that are involved in getting a product or service to the customer. These steps can include moving and transforming various raw materials into finished products, moving those products, and distributing them to the customer or end-user.
What Are the Examples of Cycle Inventory?
Cycle inventory is when you count a portion of on-hand inventory with the end goal of counting all inventory over a period of time. Cycle counting is conducted at least once during a business’s regular sales cycle, which could be two weeks, one month, three months, or longer. Below you'll find a life cycle inventory example.
Here are a few examples of cycle inventory:
- Counting all the products in a high-traffic area of the store
- Counting each product in one warehouse shelving unit each week
- Counting the inventory levels of one kind of product per week
- Verifying product types and amounts in one aisle each month
How Do You Calculate Cycle Inventory?
Cycle inventory is calculated by totaling the results from your most recent cycle count and subtracting any safety stock. For purposes of simplicity, let’s say your business only sells one kind of product. Your most recent count produces 3,781 units, 300 of which are safety stock units. This gives you a cycle inventory count of 3,481.
.jpg)
What Is Cycle Stock Formula?
You can calculate your cycle stock by adding up all on-hand inventory and subtracting safety stock. Businesses keep safety stock in the event of product demand surges, high shrinkage, or accidents. Safety stock isn’t included in cycle stock because it’s only used in unforeseen circumstances.