You might think that taking a physical count of inventory is a tedious and time-consuming task.
It certainly can be, but the benefits you get from taking it far outweigh the effort involved.
Physical inventory counting is a cornerstone of inventory control and has a massive impact on a business’s ability to limit warehouse costs and increase profits.
Here's how physical inventory works, the steps involved, why you need to take it regularly in your business, and how to calculate ending inventory.
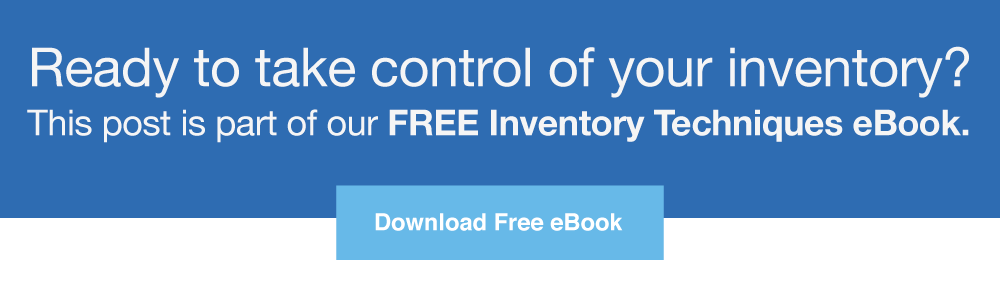
Physical Counts of Inventory
Physical counts of inventory are a vital inventory management techniques and a major skill to assess when developing an inventory manager salary. These counts uncover discrepancies in inventory records and establish the sales trends of products. Using the inventory days formula will also be necessary.
What Is Physical Inventory Count?
A physical inventory count is a method of manually counting your inventory and comparing it against recorded numbers. This count is usually performed twice, once at the start and once at the end of a reporting period.
Taking a Physical Count of Inventory
Taking inventory is best done by using a predetermined set of steps that your team can follow each time.
Here are the physical inventory count instructions:
- Plan ahead. Warehouses can contain thousands of SKUs that are spread out all over the place. The SKU number identifies the product. Determine the order you'll take inventory, create a map of the warehouse, and bucket products. This planning will help limit the amount of time wasted. You can also use ABC inventory analysis to determine the most important products to track.
- Determine frequency. You can take inventory as often as you like, but it's important that you do it on a schedule. Pick the frequency that works best for your business and that will allow you to catch problems early. And stick to it. The only way to get accurate inventory numbers is consistent counting. We recommend taking a physical count every two weeks if possible.
- Draft inventory list. This initial list will contain the products and estimated inventory levels you expect to count. It can be used to estimate the amount of time needed for the physical inventory. You should also distribute it to the team so they know what's expected. If you participate in kitting, determine if you'll count individual products or the full kits. Communicate these numbers to your online marketplace, too (if applicable).
- Choose inventory teams. Determine which team members will participate in the inventory and put them into teams. These teams can be assigned areas from the inventory plan to avoid anyone having to take the full inventory themselves.
- Prepare inventory space. Clean the warehouse and establish what areas will be used for taking inventory. If small items will be counted, set up tables and bins to use during the count.
- Freeze all other activities. A full physical inventory requires you to stop other operations so that you don't throw off the count. You don't want staff picking and packing while you're trying to establish the inventory on-hand.
- Take inventory. Finally, it's time to actually go through the list and count each product in your warehouse. Tally these up against the numbers in your system to uncover any areas where improvement is needed. Be sure to also calculate turnover with the inventory turnover formula.
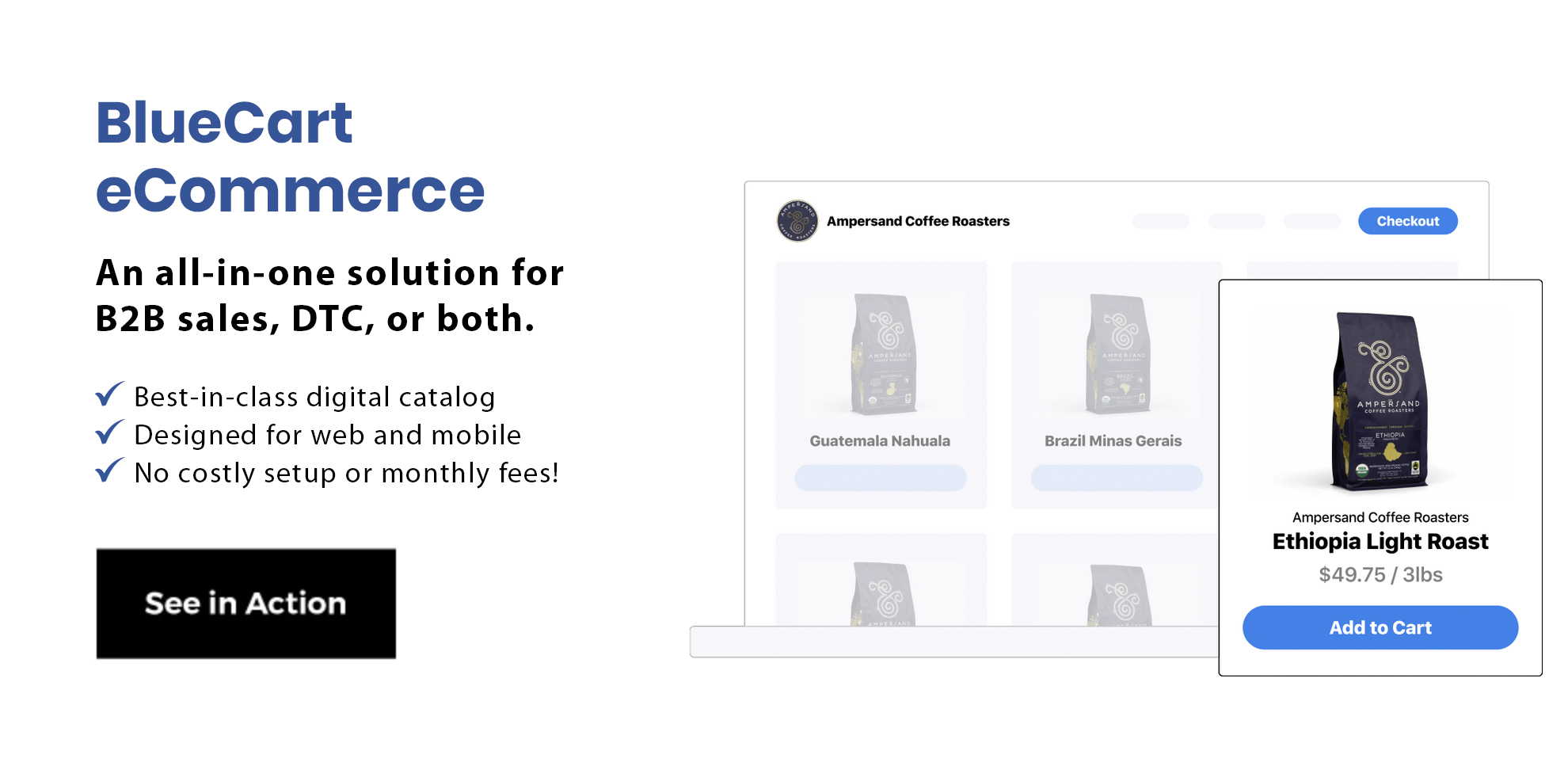
When Is a Physical Inventory Usually Taken?
A physical inventory count is usually taken both when goods are not being sold or received and at the end of the company's fiscal year. You can, of course, take it more often to ensure greater accuracy.
You may also choose to invest in a perpetual inventory management platform or ERP software (see benefits of ERP). These platforms offer access to data at all times and automatically update as products are added or removed from your inventory.
For bar and restaurant owners, BinWise Pro is the best solution. It helps you manage the entire lifecycle of your beverage inventory. It can even be integrated into a POS system for better accuracy.
Why Is Physical Inventory Important?
There are many reasons why taking a physical count of inventory is important to your business.
Here are a few:
- Uncover inventory issues. There are many problems that can be revealed during a physical inventory. You may have excess inventory leading to dead stock (see dead stock meaning), or low levels of inventory will lead to a product being on backorder. Finding these issues earlier can prevent them from causing more trouble down the road and let you know if it's time to do some inventory reduction.
- Ensure accounting accuracy. The last thing you want as a business owner or manager is an accounting or inventory audit. If your inventory numbers are off, so is your accounting and this can only lead to trouble. Consistent inventory can prevent numbers from being off and allow you to save money.
- Order planning. Counting and tracking inventory trends will help inform your products' reorder point (using the reorder point formula). By ordering product at the correct time, you can avoid having too much standing inventory. This will save you money and ensure you have the product to meet demand. This is especially important if you use a slow transport method like bulk shipping.
Physical Count vs Cycle Count
A physical inventory involves counting all products in storage, while an inventory cycle count involves only counting a handful of products. These counts are simpler to perform, can be done without stopping other operations, and can be performed only on your most valuable products. However, it does require performing counts more often and will not give you insight into your full inventory numbers.
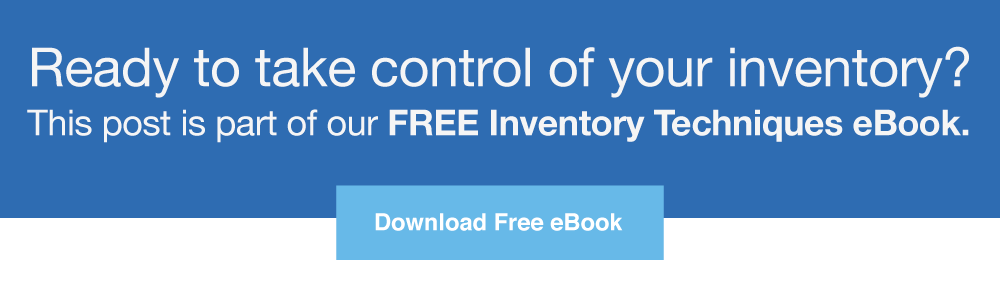
Let's Get Physical
Physical inventory counting allows you to better understand your inventory and avoid costly issues. It will inform you of the correct quantities to order and when you should do so. Physical inventory counts are key in getting the most value out of your products.
One way to limit the amount of physical inventories needed is to use a just in time inventory system if possible. This will limit the amount of time inventory spends in your warehouse and streamline processes.
Frequently Asked Questions About Physical Counts of Inventory
Physical counts of inventory may not be the most fun thing, but they're still an important part of business and warehouse management. Dive deeper into how it works with these commonly asked questions and answers:
What is included in physical inventory?
A physical inventory count includes raw materials inventory, work in process inventory, and finished goods inventory. These categories comprise the goods a company uses to produce merchandise inventory, which is any product or item ready for sale.
Physical inventory includes counting the volume, weight, number, and other measurements of each inventory unit. These metrics are compiled to determine a company’s balance sheet, which shows all the assets and accounts receivable of a business.
What are the different types of inventory counts?
There are four types of inventory counting: full counting, cycle counting, tag counting, and ad hoc counting. Full counts are a total review of all products in a warehouse or store. This includes goods on warehouse shelves, product shelves, products currently being stocked, and everything in between.
Cycle counting is counting all the products in a designated area of the store, or a particular type of product. You then move from one zone to the next until the entire store is counted within a time period. Cycle counts are most effective in high traffic industries, like grocery and retail.
Tag counting is the same as an inventory cycle count or full count, simply with tags assigned to products. Counters add product info to each tag, and at the end of the count, staff checks the tag information against system data.
Ad hoc counting is used on the fly for areas of concern, or products that are going to be updated soon. With this method, employees count whichever items they’re assigned and update the inventory data in their warehouse management system.
Do you know when should a physical inventory be taken?
Physical inventory counts should be taken periodically for best results--typically quarterly or bi-monthly. Counting too frequently is unproductive and will produce similar results, but counting too infrequently increases the chances of missing critical information. If you count inventory and find you need to cut back on expenses, SKU rationalization can benefit overall costs long-term.
If you have a small business or warehouse, a full inventory count every six months may be all you need. If you own a franchise or have a large operation, physical inventory counts every two to three months may be needed.