There is no successful inventory management process operation that doesn’t first master the acquisition and careful usage of its raw materials. Literally, there is none. Because it’s impossible.
Most businesses are in a race to acquire the lowest-cost material and drive operating costs down as far as they can. It’s not easy because it requires anticipating supply chain behavior. This is true for both B2B vs. B2C businesses.
And that all starts the management of your raw materials. Your inventory turnover ratio, inventory days, COGS, and profitability all depend on effectively managing your raw materials inventory. It benchmarks your entire inventory management process.
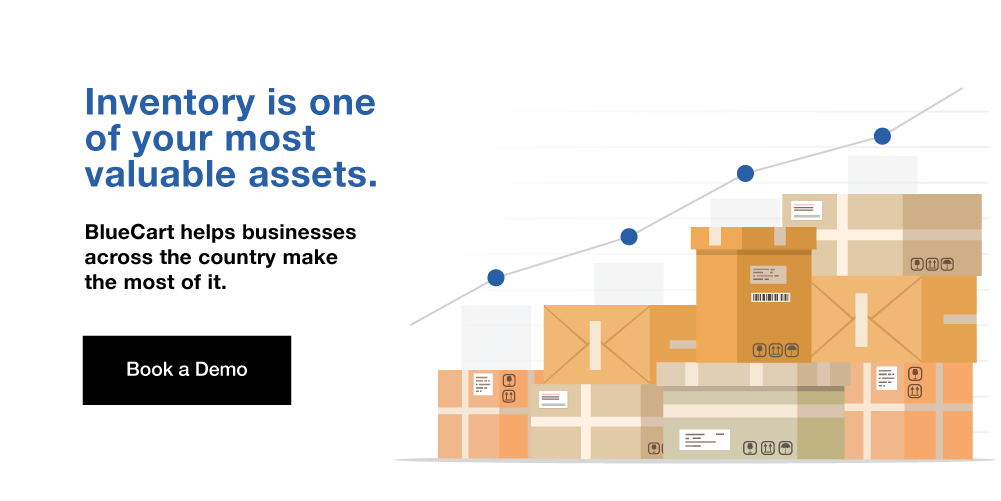
What’s more, raw materials have a big impact on the overall health and eCommerce accounting of your company. That’s because they’re recorded as a current asset on your balance sheet. It gives them an outsized impact on cash flow and end-period financial performance.
Raw materials, then, are the untouched clay of business, ready to be molded into economic art. Here’s what you need to know about them.
What Is Raw Materials Inventory?: Raw Material Inventory Definition
The raw material inventory definition is stock that hasn’t yet been used for manufacturing. Oftentimes business owners will obtain materials from an online marketplace or wholesale directory. Just make sure the businesses you purchase from have a valid wholesale license to avoid getting burned. Carefully review the terms of the wholesale purchase agreement to understand legalities and policies.
It has yet to be combined with human labor and turned into either work in process inventory or finished goods inventory, which are the two other types of manufacturing inventory. If you’re just getting started learning about what is inventory, make sure to read about the basics first.
That’s why the raw material inventory definition varies by company. It refers to the pre-production inventory—and that depends on what a company’s finished product is. There are two types of raw materials inventory: direct and indirect.
Direct Raw Materials Inventory
Direct raw materials are all the materials that actually constitute the finished product. Take a coffee roasting or coffee brewing business, for example. Their finished product is roasted coffee beans, and their raw materials inventory is green coffee beans.
Consider also a coffee machine manufacturer. Their finished products (or merchandise inventory) are functional coffee machines. Their raw materials inventory are the glass, plastic, and electric components that make up a coffee machine.
Likewise, think of the cotton used to make cotton shirts or the glass used to make windows. This all needs to be considered when they price their monthly coffee subscription.
Indirect Raw Materials
Indirect raw materials inventory are all materials consumed during the production process but are not a part of the finished product. This includes things like disposable tools and protective equipment, light bulbs, cleaning supplies, fuel, and lubricants.
How to Calculate Raw Materials Inventory
To figure out how to calculate raw materials inventory, you’ll need to know:
- Beginning Raw Materials Inventory
- Raw Materials Purchased
- Cost of Goods Sold (COGS)
It's not so different from how to calculate finished goods inventory.
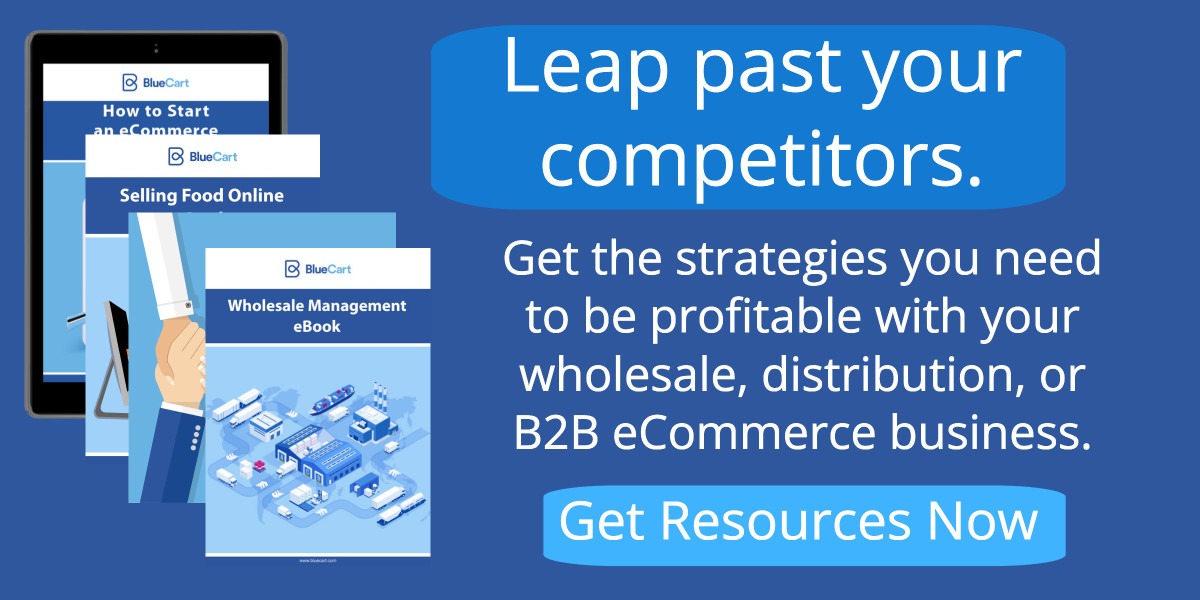
Beginning Raw Materials Inventory Formula
Remember that beginning raw materials inventory is the previous accounting period’s ending raw materials inventory.
To find your beginning raw materials inventory, you’ll need to determine a more exact figure than you would with an average inventory formula. To determine the raw material inventory, use the following formula:
Beginning Raw Materials Inventory = (COGS + Ending Raw Materials Inventory) - Raw Materials Inventory Purchased
How to Find Ending Raw Materials Inventory
Ending raw materials inventory is often what businesses are out to calculate. Keep in mind that ending raw materials inventory will be the beginning raw materials inventory for the next accounting period.
Here’s the ending raw materials inventory formula:
Ending Raw Materials Inventory = (Raw Materials Inventory Purchased + Beginning Raw Materials Inventory) - COGS
Let’s use a clothing manufacturer as an example. Consider BlueCart Tee Shirt Co. They make and sell cotton tee shirts.
They have a beginning raw materials inventory of $10,000. That’s $10,000 worth of cotton and the expendable resources used to turn cotton into shirts. Over the accounting period in question, they acquire $15,000 worth of raw materials. And, during the accounting period, $7,000 worth of finished goods was sold:
Raw Materials Inventory = $10,000 + $15,000 - $7,000
Raw Materials Inventory = $18,000
This means the total cost of all pre-production material BlueCart Tee Shirt Co. has on hand at the end of this accounting period is $18,000.
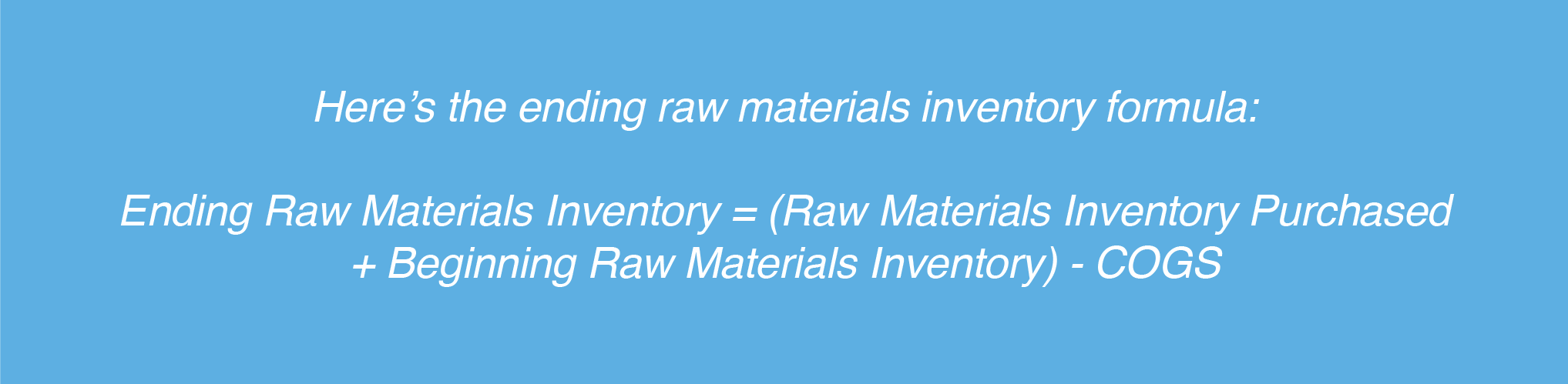
How to Calculate Raw Materials Inventory Turnover
Raw materials inventory turnover represents the rate at which raw inventory is used and then replaced. It’s a reliable measure of how accurate a business’s inventory forecasting and purchasing strategies are.
The raw materials inventory turnover ratio equation for a given time period is is:
COGS / Average Cost of Raw Materials Inventory
Where the average cost of raw materials inventory is:
(Beginning Raw Materials Inventory + Ending Raw Materials Inventory) / 2
An inventory turnover ratio of between 4 and 6 is considered an ideal balance between sales and replenishment. A raw materials inventory turnover rate higher than that means that a company’s raw materials are used and replaced frequently. Though that may also indicate a potential for costly backorders.
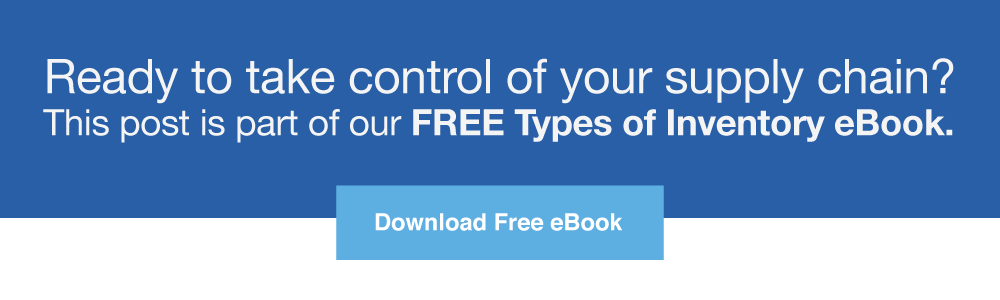
A lower rate materials inventory turnover, alternatively, means that demand planning and purchasing planning are not properly coordinated. It is a vital part in a company's ability to hit their inventory KPI.
Raw Materials Inventory Accounting
Accounting for raw materials accurately helps businesses track that investment throughout the production process. That, in turn, gives an accurate picture of a company’s financial health. It all starts with tight raw inventory bookkeeping.
When raw materials are used up, the bookkeeping depends on whether they’re direct or indirect raw materials. Just make sure you know the difference between markup vs margin when setting the wholesale price for each product you create.
What Kind of Asset Is Raw Materials Inventory?
Raw materials inventory is kept on the balance sheet as a current asset. Initially, acquired raw materials of all types, both direct and indirect, are recorded with a debit to the raw materials inventory account and a credit to accounts payable.
Accounting for Direct Raw Materials
If you use direct raw materials, debit the WIP inventory account and credit the raw materials inventory asset account. Since there are key differences between both accounts, make sure to use an efficient accounting resource to decipher similar debits and credits.
Accounting for Indirect Raw Materials
If you use indirect raw materials inventory, debit your overhead account and credit the raw inventory asset account. Then, at the very end of the accounting period, the ending overhead balance is placed into COGS.
Accounting for Unusable Raw Materials Inventory
Sometimes, sadly, raw materials become so obsolete or degraded that they can no longer be used. Unsellable stock is often referred to as dead stock. The dead stock meaning refers to anything from expired raw materials to off-season goods. When this happens, the cost is usually allocated directly to the COGS, with a credit to the raw materials account. This isn't affected by your inventory costing methods.
Raw materials make up the final product; therefore, it’s unlikely that a company can sell excessive stock as bundles, or by using the kitting method. With this in mind, it’s crucial to avoid overstocking raw materials and not allowing enough lead time in between ordering points.
Challenges in Raw Materials Inventory Management
Management of raw materials inventory can be a challenging task. There are a lot of risks and things to consider. Let’s examine the main challenges in raw materials inventory management.
- Planning. Inventory planning is paramount when it comes to raw materials inventory management. That’s because of the fluctuating prices of different raw materials. Poor planning can lead to overstocking and increased warehousing costs or understocking and missed opportunities to fill orders. One of the best ways to handle this challenge is by investing in proper solutions for demand forecasting.
- Supply chain disruptions. Carefully picking suppliers and partnering with distributors that have good supply capabilities can be the solution to supply chain disruptions. Make sure to have backup plans and safety stock levels on all important raw materials.
- Quality control. Poor quality of raw materials will result in poor quality of the final products. Thus, manufacturers need to have proper quality control procedures for incoming raw materials. A potential solution for this raw materials inventory management challenge is to partner with distributors that have well-established market presence and quality assurance protocols.
- Capital constraints. Purchasing large quantities can lead to lower prices per unit. However, budgetary restrictions are the reason why some companies can’t afford to benefit from these discounts. Minimizing the cash restrained in other stock and having a high inventory turnover rate can allow businesses to negotiate better prices.
7 Tips on How to Manage Raw Material Inventory
At the risk of droning on: efficient inventory management starts with smart raw material inventory management. Without the right tools in place, supply chain managers run the risk of of excessive stock and expenses. Here are seven tips for how to manage raw material inventory.
1. Use a Material Resource Planning Platform
Material planning is the science of determining the types and quantities of raw inventory needed for production. Both direct and indirect raw materials need stores of safety stock, buffer stock, and anticipation stock.
Material Resource Planning (MRP) platforms analyze historical consumption data, lead time, modes of production, and supply chain complexity. Be sure that you learn what the ERP meaning refers to, and how it differs from MRP. They balance those with future forecasts to suggest optimal stock levels and purchasing cadences. This can work for other types of inventory, too, like MRO inventory.
2. Keep an Eye on Overstock and Understock
A balance of available stock and upcoming orders is a sign that you’re properly managing your inventory. Understock can hinder a business, as it can cause major delays. Whether it results in time constraints between the raw materials’ source and the manufacturer, or the factory and retailer, understock can result in skewed timelines.
On the flipside, overstock can lead to a rise in the overall carrying cost. There are various expenses that go into inventory storage. For instance, some raw materials–especially within the food and beverage industry–have to be kept in specific environments. If your warehouse is overstocked, this can lead to surpassing expiration dates and spoilage. It also increases overhead expenses, as these materials require electrical appliances.
Other common variables that can lead to overstock-related costs include transporting the materials to another facility, repositioning products for delivery pickups, and time spent on labor. The labor cost can take up a large portion of your budget, so keep an eye on this metric. Be sure to take all of these scenarios into consideration before restocking raw materials.
Such expenses often result in a decrease of profit margin, which affects short and long-term business goals. Calculating projections can guide supply chain and business operations, which require steady numbers. So, always store the proper amounts of stock to predict clearer estimates.
Perhaps unsurprisingly, overstock or understock means your raw material inventory management isn’t optimized.
If you have overstock, it means:
- Your sales forecasts are too optimistic. Try using demand planning software to help better predict when to place upcoming orders.
- Your estimated lead times are too high. If you’re projecting a much lengthier amount of time from the time of product initiation through its delivery, the amount of stock in the warehouse can build up. By lessening the lead time, you can speed up the inventory turnover rate.
- Your safety, buffer, or anticipation stock should be reduced. Not only will reducing stock save you a significant amount of carrying costs, but it will assist in streamlining warehouse operations.
If you have understock, it means:
- Your forecasting failed to identify seasonal demand trends. Conduct frequent market research to determine when you should order seasonal materials. Use historical data and industry trends to determine which seasonal stock is right for your product lines.
- Lead times are taking too long due to pipeline inventory issues like transport delays, customs, or other freight complications. If this becomes an issue, look at past records to figure out what your average lead time is. The data you find can be useful in scheduling future deliveries.
Shortages from suppliers upstream in the supply chain. If you’re finding that material shortages are negatively impacting your supply chain’s timeline, consider partnering with a different supplier. For instance, inventory management apps allow companies to browse materials from multiple suppliers. Plus, a platform like this will allow you to minimize the time it takes to place orders.
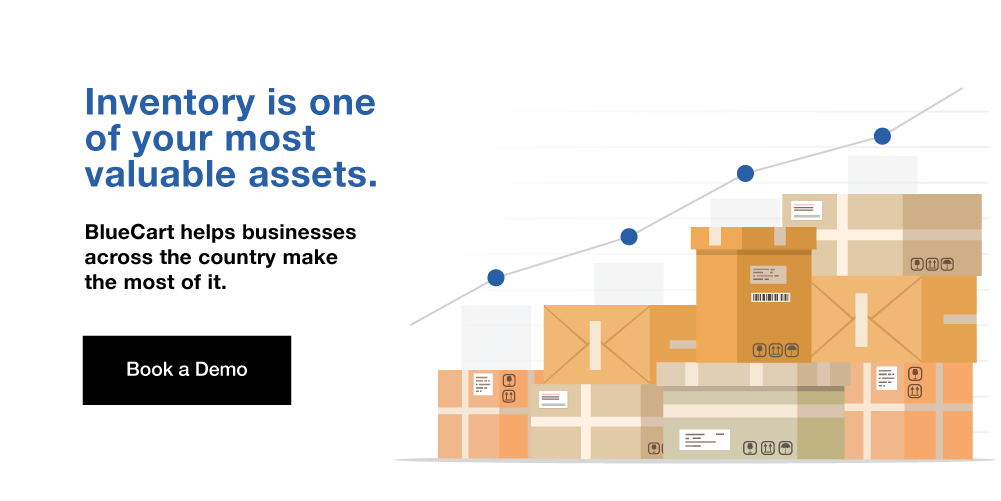
3. Mind Quality Control
It’s not uncommon for a manufacturer to reject raw material from vendors due to quality or compliance (for electronics, for example) issues. Even if that manufacturer is in a current vendor managed inventory (VMI) agreement with them. In those cases, an inventory shortage is all but inevitable.
Try not to cut costs on raw materials because the resultant costs of added labor and paused production—not to mention customer satisfaction—will dwarf it.
4. Automate Data Management
This is probably the most impactful decision you can make. Modern global supply chains are ridiculously complicated. There is no industry where manual inventory management and analysis cuts it.
Find an automated tool that offers:
- Demand forecasting. Utilize efficient software to interpret historic data and make estimates for customer demand. By having such forecasts as part of your inventory management strategy, you’ll be able to prioritize raw material orders much more effectively. Plus, accurate decision-making processes will help businesses simultaneously save money and increase profits.
- Expansive data collection and analysis that collects data from all parts of the supply chain. The supply chain contains numerous data points pertaining to inventory, demand, and price estimations. An automated data-mining tool can streamline these analyses, making it easier to track various metrics. Trends, alerts, and order dates are just a few of the numbers you’ll want to analyze on a semi-regular basis, so it’s a good idea to automate the whole process.
- Intelligent costing functions to estimate the total manufacturing cost and inventory carrying cost. These costs are two of the most significant figures to determine upon placing orders for raw materials. Companies can end up losing a large portion of total revenue from the costs of storing inventory. If for any reason, certain items aren’t selling or being used during production, warehousing costs can increase in no time.
- For food and beverage businesses, hospitality software that tracks product origin and provenance is often necessary. In some cases, this data will be necessary to abide by health and safety regulations. Such information might include key points like “may contain” labels for food allergies, or special notes regarding other types of dietary restrictions. By obtaining this information for a food and beverage company, you’ll also be able to properly label food items. In doing so, there’s potential of selling to a wider customer base or niche market.
- Route optimization software can help eliminate too much time in transit. To maintain efficiency, warehouse staff should be aware of delivery routes (learn more about what is a warehouse associate). Depending on a business’ time restraints and sales goals, route optimization software can help manage the schedule around fleet timelines.
5. Focus on Raw and Finished Inventory First
Small- to medium-sized businesses are often overwhelmed by inventory management. So they do what they’re used to: try to do everything all at once. Don’t.
The lowest hanging inventory fruit for SMBs is raw material and finished goods. Focus on those first, then move on to tweaking your production process with WIP inventory optimization. But don’t go for WIP analysis first.
By analyzing pre and post-production inventory, you’ll implicitly get a picture of your WIP inventory. Only after you’ve mastered raw and finished goods inventory should you slowly turn the screw on WIP inventory analysis.
6. Calculate Reorder Points for Safety Stock
Don’t replenish safety stock on a whim. Calculate hard reorder points so you know exactly when to order more safety stock. It’s the best way to ensure you’re not running out of inventory. And it lessens the cognitive load of inventory management. When you’re aware of each reorder point, there’s no thinking involved. When you hit a predetermined inventory level, you reorder.
7. Don’t Account for Literally Everything
Some manufacturers have many different kinds of low-cost raw materials. So much, in fact, that accurately accounting for and tracking everything isn’t reasonable. It won’t have major effects for costs long-term, and it’s not the most efficient area of work to invest time.
While high-cost raw material inventory should be on your production recipe or bill of materials, low-cost, indirect materials need not be accounted for precisely. Think of boxes upon boxes of individual screws. Feel free to cost something like that when they’re acquired en masse. That way you don’t have to worry about every single little piece during production.
Raw Materials Inventory Management: Find the Middle
How to manage raw material inventory is all about moderation. Don’t make the mistake of thinking that having a bunch of extra raw materials lying around is insulating you from catastrophe.
Cash tied up in sitting inventory like that could be weighing your business down in fatal ways. Perform a consistent inventory audit to avoid issues with managing raw inventory and always keep an eye on your fill rate. The only way to be sure it’s not is to spin up a raw material inventory management process so sound, so strategic, that there are zero doubts.
Think of raw materials like food. Your business needs them to survive. But too much or too little can cause problems. That’s why virtually every manufacturer today relies on inventory management software to find a healthy middle ground.
Increasing your sell through rate and lowering inventory shrinkage can also help lower the raw materials that build up in your storage. This is made easier by using a B2B eCommerce platform or a vendor marketplace. Even better, you can choose to use the dropshipping model so you never deal with raw materials or inventory again.
Frequently Asked Questions About What Is Raw Material?
It’s important to see raw materials inventory as a pivotal part of your entire inventory plan. Here are some commonly asked questions and answers about it:
How Do You Find Raw Materials Inventory?
Raw materials inventory is found by researching suppliers and choosing one that’s a good fit for your business. You can research options in a wholesale directory, which is any website that lists wholesale suppliers and the goods they sell.
Another way you can find raw materials inventory is by asking fellow business owners where they source materials from. If you’re in good standing with them, people are often willing to share their professional network and personal tips.
Do Raw Materials Count as Inventory?
Yes, raw materials absolutely count as a form of inventory. Any partial product, material, or other physical good that’s used to make a finished good is considered inventory.
To keep your raw materials from being categorized incorrectly, though, it’s wise to have an inventory management system. This way your warehousing staff knows where each type of item is and how many are in stock.
How Do You Record Raw Materials Inventory?
Raw materials inventory is usually recorded as an inventory asset on a balance sheet. When the raw materials are received, an accountant or financial analyst will record this data in their software.
The raw materials inventory account is debited and the supplier the business needs to pay is credited in the supplier’s accounts payable account. This system ensures raw materials aren’t lumped in with work in process inventory or other goods.
What Is an Example of a Raw Materials Inventory?
From wheat and soybeans to steel and wood, businesses use hundreds of different raw materials. It all depends on the type of business and the final products it manufactures. In many cases, one company’s end product can be another company’s raw material. For example, a steel producer uses iron ore to make its end products. This steel is then used by car manufacturers to make vehicles. Here are some examples of raw materials inventory.
- Metals and minerals;
- Agricultural products such as grains, produce, and other farm products;
- Cotton, wool, synthetic fibers, and other textile products;
- Paper products;
- Plastics;