Demand for your products can rise and fall at any moment. You need to be prepared for such eventualities.
Do you have stock sitting in your inventory (see what is inventory) slowly depreciating or find yourself lacking the materials to keep up with customer needs? Maybe it's time you looked into a just in time inventory management system.
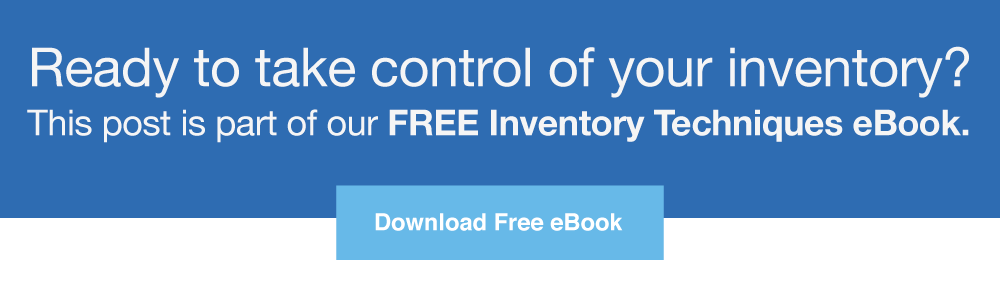
Just in time inventory (JIT) can keep costs low and allow you to operate your cycle inventory to meet demand. Here's how it works and how you can adopt the strategy for your business.
Just In Time Inventory
Just in time inventory offers businesses a chance to streamline their purchasing, ensure a steady stream of supplies, and keep inventory costs low. It limits the amount of product on-hand and limits the risk of dead stock and backordered products.
So, how does it work and who should use it?
JIT Meaning: What Does JIT Mean?
JIT, or just in time, is an inventory model where the raw materials you use or products you sell are delivered to your warehouse only as you need them. This involves staying in constant contact with your suppliers to ensure goods arrive at the optimal time. Many manufacturers choose this model to streamline their processes and save valuable resources.
What Is Just in Time Inventory?
Just in time inventory is stock that arrives in your inventory as you need it for production or sales. With JIT, instead of having a large amount of merchandise inventory or raw materials inventory, you have a much smaller rotating stock. This stock is ordered with the intention of using immediately upon arrival and will spend as little time as possible on your premises. In that sense, it's opposed to bulk shipping or bulk inventory.
Who Should Use A JIT System?
JIT systems are not beneficial to all businesses. Many newer businesses shouldn't adopt the model as they don't have a sufficiently built supply chain to handle a JIT system. It's important to evaluate how it would affect your operations before adopting the model.
JIT systems are most successful for businesses that have the following:
- Short production times.
- Streamlined supply chain management.
- Accurate demand and inventory forecasting.
- Efficient order fulfillment, including batch picking
- Reliable supply chain.
- Inventory management software.
If your business meets all these criteria, the JIT system might be the right choice for you. If not, look into which are lacking and work on improving the current system you use. If your suppliers can't meet demand in a timely manner, you don't want to switch models and be left without products to sell.
.jpg)
JIT Manufacturing: Just In Time Manufacturing
The just in time inventory model is very common in the manufacturing industry. Since production costs are tied directly to a manufacturer’s ability to survive, any savings there give the business a better chance of success. By receiving raw materials only as needed for production, a manufacturer can save money on storage as well as avoid issues with dead stock or decoupling inventory.
JIT manufacturing is also similar to lean manufacturing in that it helps eliminate wasted efforts by employees and lets you cut out processes and areas that are unnecessary. By manufacturing only what demand requires, production costs go down while production quality goes up. This, in turn, leads to higher customer satisfaction and better sales.
Just in Time Inventory Management Process
Just in time inventory management requires planning and forethought to avoid running into supply shortages. Since inventory arrives only on an as-needed basis, you must always be aware of expected sales and the amount of time it takes for your goods to be ready for sale. You must also be flexible and ready to respond to sudden shifts in market demands.
Just in Time Inventory Control Model
The just in time inventory control model allows a business to quickly respond to shifts in customer needs and reduces the number of unsold or outdated products. This model is best used for businesses that have shorter demand spikes. It is often used by the foodservice industry, technology manufacturers, and book publishing. These industries need to make product quickly to keep up with demand and avoid excess inventory when that demand falls.
JIT: Just In Time Inventory System
A just in time inventory system, or JIT system, is an inventory strategy where raw materials and supplies are ordered and received as they're needed. The just in time system requires a strong relationship between the retailer, an online marketplace, and the supplier. It is unlike the just-in-case inventory system. In that system, you order and store safety stock in the event demand surges or you run into production problems.
Characteristics of Just in Time Inventory System
The just in time inventory system has a number of characteristics that set it apart from other inventory systems.
Here are a few common ones:
- Smaller deliveries received more often. These deliveries can be daily or even hourly as needed to keep the production or sales process going and keeping up with demand.
- Higher supplier quality. Since you don't have time to inspect goods every time they arrive, JIT suppliers are usually certified for quality. This means you can trust the materials that arrive are up to standard.
- Unique work arrangements. JIT production areas need to be more flexible than normal production. This means they are smaller and allow in-process goods to be passed from each work center quickly and efficiently.
- Cross-trained employees. JIT employees are often certified to work on different tasks within the production process. This gives them more work to do and cuts costs to the business like the cost of physical counts of inventory.
- Immediate fulfillment upon completion. There is little storage for completed goods or materials. As such, once you finish a good, it is immediately placed on a truck for shipment to the customer.
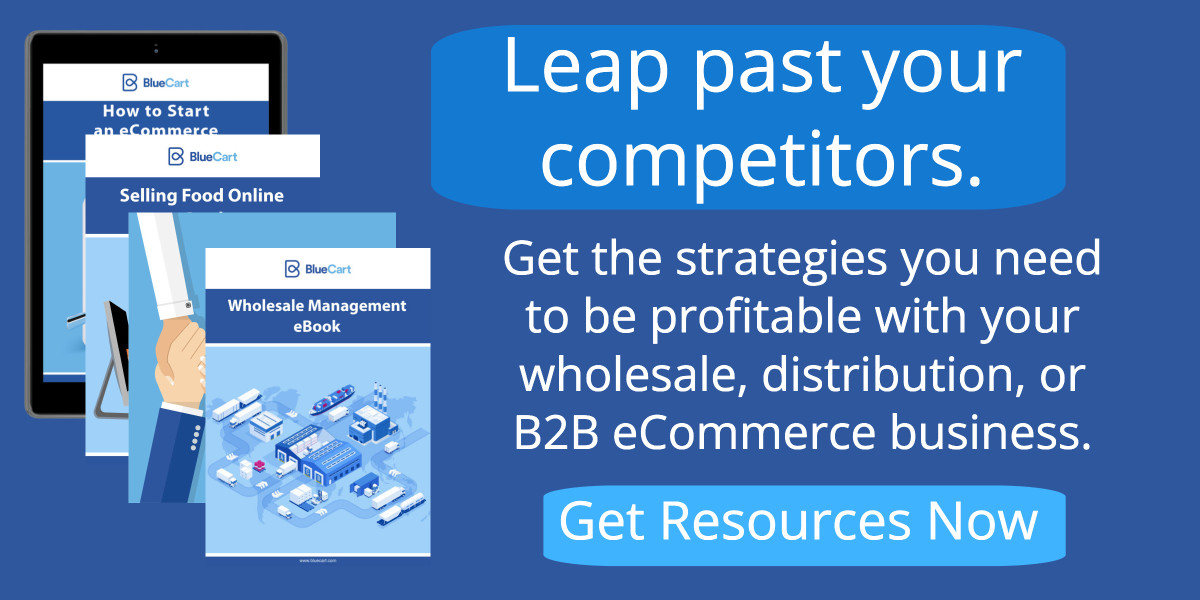
Just in Time Inventory System Example
The just in time inventory system isn't as complicated as it may sound.
Here's an example of how it works:
- You receive an order for 14 widgets from a customer.
- You place an order with your supplier for the materials needed to make only those 14 widgets.
- The supplier immediately loads a shipment and sends it to your facility.
- Your team receives the materials and immediately begins production.
- The goods are passed from station to station until completed.
- Once all 14 widgets are finished they are put into a shipment and sent directly to the customer.
If any other orders come in during that production time, the same steps are followed. This keeps the production chain moving quickly and keeps excess inventory from building up in your warehouse.
How to Make A JIT System Work for You
If you decide to adopt the JIT system for your business, there are a few things you can do to get the most out of it.
Here are our top three recommendations on how to make a JIT system work for you:
- Establish and track eCommerce KPIs. By setting measurable goals and tracking demand trends you can stay on top of your ordering. This will ensure the JIT system is successful and avoid issues with inventory levels. This will also prevent causing bullwhip effect in supply chain and upsetting your suppliers.
- Build strong relationships with vendors. The JIT model requires consistent communication with your vendors. Work with them to establish a good relationship and share information as often as possible. This will keep you ahead of issues with lead time and avoid running into problems meeting demand.
- Invest in good inventory management software. Keeping track of your inventory is more vital than ever with a JIT system. Use a perpetual inventory system with robust reporting. This will ensure you are aware of any issues with supplies and can act as quickly as possible.
Advantages & Disadvantages of Just in Time Inventory
As with all inventory management techniques, using a just in time inventory system has both advantages and disadvantages.
Advantages of JIT Inventory Management:
- Shorter production runs. Manufacturers no longer need to build up large amounts of manufacturing inventory as the product life cycle is shorter in JIT. This also allows the retailers to limit their offerings and put their full focus on only a few products youkeep on-hand for fewer inventory days.
- Easily switch between products. If a product has issues or doesn't sell well, you can easily shift your efforts to one that does. This agility is key to maximizing sales and profits.
- No need for extensive warehousing. Since inventory arrives only as you need it, you don't need a large storage space for work in process inventory. This saves a lot of money and energy that you can channel into growing your business.
- Lower material costs. Since you only pay for the material as you need, you avoid excessive costs for materials that sit in storage waiting to be used. You also suffer less waste and shrinkage. This can help you hit your target inventory KPI more easily.
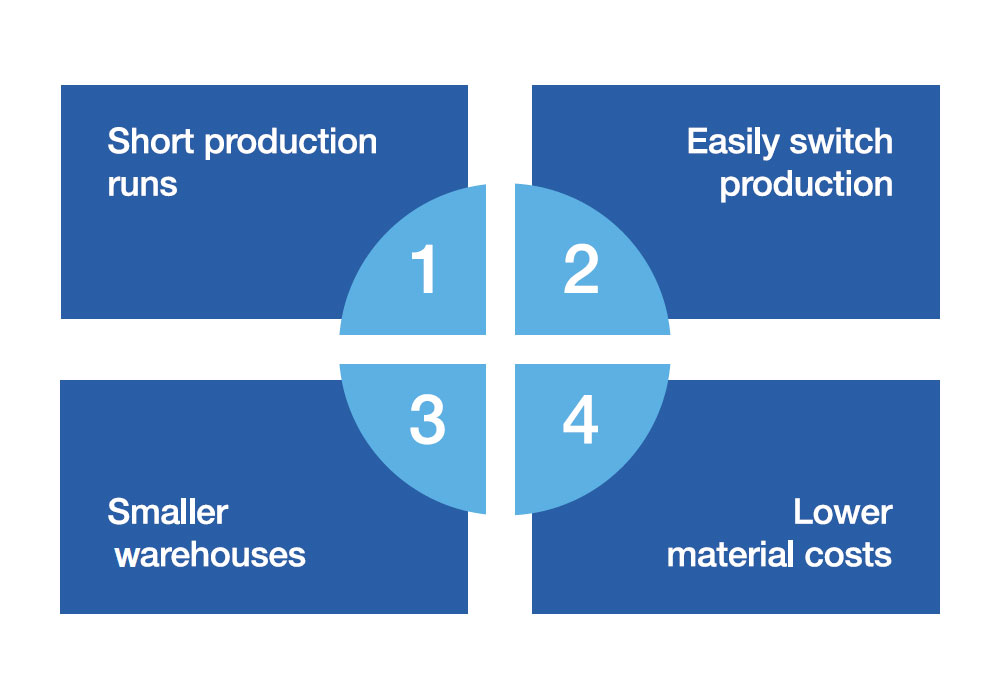
Disadvantages of JIT:
A disadvantage of the JIT inventory system is the ...
- Requirement of more planning. Since you don't have stock sitting around, you need to order the correct amount every time. This requires a lot of planning and insight into your sales trends.
- Risk running out of inventory. If there is a sudden increase in demand, you risk not being able to meet it. This means you'll miss out on sales and upset your customers. This is made even worse if the goods you need are out of stock (read more about backorder meaning). It may also be more difficult to pull off kitting.
- Lack of control over time frame. No matter the inventory method, you always rely on manufacturers and suppliers to control their production time frame. With JIT inventory, since you don't have any extra stock, this can come back to bite you.
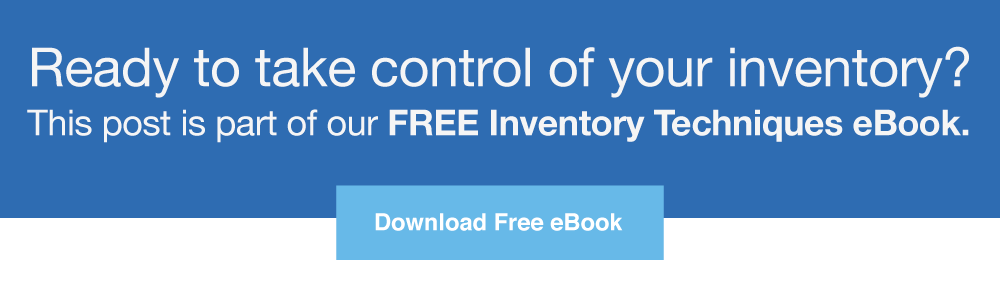
Quiz: A Just in Time Inventory System Usually Reduces Costs for...
Were you paying attention to how a just in time inventory system works? Let's find out with a quick quiz.
A just-in-time inventory system usually reduces costs for:
A. Both the producer and its suppliers.
B. Neither the supplier nor the producer, though it does lead to more flexibility for both.
C. The producer, but not its suppliers.
D. The suppliers, but not the producer.
If you chose C, you’re correct. The producer sees lower cost under the JIT inventory system, while the suppliers see little change. Nice work!
Did This Help You... Just In Time?
Did we convince you to use a just in time inventory management system? Now that you know more about it, you can make an informed decision about what works best for your business. ABC inventory analysis may also be of interest. Whatever the case, don't leave money on the table and look into new ways to lower costs, boost your sales, and grow your business.
Other methods for eliminating waste and saving storage costs is by using dropshipping or consignment inventory. You can compare these two inventory models and see what might work for your business so you can focus on growing sales.