As savvy business owners and supply chain management enthusiasts, it's crucial to understand the ins and outs of inventory management, and finished goods inventory is no exception. In this comprehensive blog, we'll dive deep into the intricacies of the finished goods inventory formula, revealing the secrets behind calculating your stock like a pro.
Get ready to explore the world of finished goods produced formula, as we break down each step on how to calculate finished goods inventory, and ensure that your business remains efficient and cost-effective. But that's not all!
We'll also delve into the significance of inventory turnover and provide valuable insights to help you optimize your stock management. Whether you're an industry veteran or a newcomer, our easy-to-follow guide will equip you with the knowledge you need to excel in managing your finished goods inventory.
Here’s what accurately reported finished goods inventory helps you do:
- Reduce waste
- Determine profitability
- Optimize the inventory management process
Those are three very good things. And they all improve when you invest in tightening up your finished goods inventory process and reporting (see what is inventory).
So let’s get down to business. Here’s what finished goods inventory is, how to calculate it, and why it's one of the best types of inventory out there.
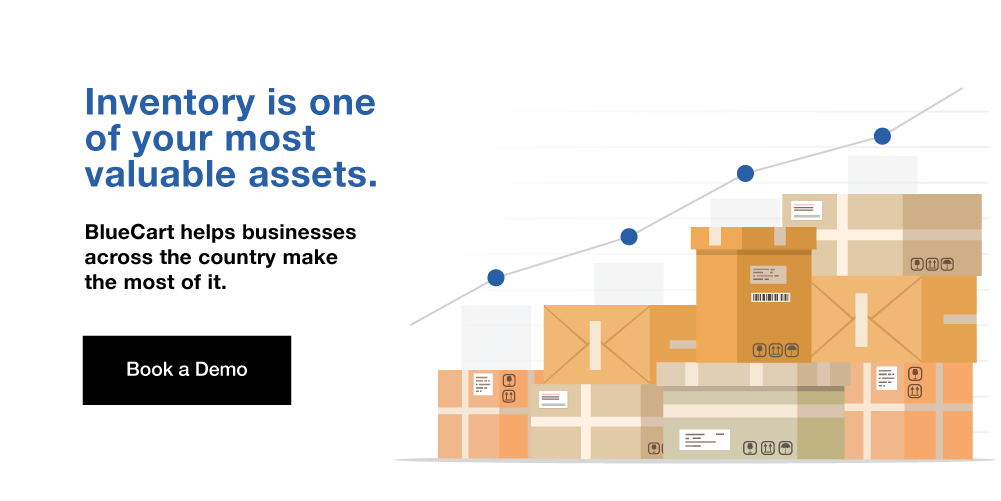
What Are Finished Goods?
Finished goods are the final products that manufacturers sell to buyers, such as upstream vendors or retailers. They are the culmination of raw materials and items in every stage of production. It’s also known as finished product inventory.
"Finished goods inventory", also known as "finished product inventory", is a term that can vary depending on the context.
One manufacturer's finished goods inventory may be a retailer's merchandise inventory, dropshipping inventory, or another manufacturer's raw material or component. The destination of these finished goods determines their classification after completion.
Becoming Finished Goods Inventory: The Journey from Raw Materials to Finished Goods Inventory
To better understand the finished goods produced formula, it's essential to grasp the entire manufacturing process. Finished goods inventory becomes finished goods inventory by first being the other two types of manufacturing inventory.
There are three main steps involved in transforming raw materials into finished goods inventory. Here’s how it all goes down:
Step 1: Raw Materials Inventory
Raw materials inventory is all the ingredients or base component parts that will be used in the production process. They’re considered raw materials inventory until they’re combined with human labor. At that point, the inventory is no longer raw. It’s been moved out of its initial warehousing environment and is now a work in procress.
Step 2: Work In Process Inventory
Work in process inventory (AKA work in progress or WIP inventory) is everything that happens to inventory in between raw materials and finished goods. This is when the actual manufacturing is happening.
There are some very short or simple manufacturing processes that don’t require specific reporting of WIP inventory. In those instances, companies move straight from raw materials inventory to finished goods inventory.
Step 3: Finished Goods Inventory
When the manufacturing process is finished, the work in process becomes a finished good. Finished goods inventory is what manufacturers depend on to generate revenue. Once finished, these goods can ship and it's time to focus on inventory tracking. Most of these goods are also assigned a SKU number.
Key Characteristics of Finished Goods Inventory
There are a few attributes that best describe what finished goods inventory is. Let’s examine their main characteristics.
- Completed and ready for sale. The finished goods inventory is 100% ready to be sold and liquidated. This stock is stored in warehouses in inventory areas designated for finished goods inventory.
- Finished goods inventory value. The value of these products in balance sheets includes raw materials, labor, and other expenses during the work-in-progress stage of the process.
- Impact on cash flow and liquidity. Finished goods inventory has the highest impact on revenue. Having insufficient levels of finished goods means that the business is missing opportunities to sell and generate revenue. High levels of finished goods inventory mean the company has too much capital tied up and needs to liquidate its stock through more investments in marketing and advertising. Of course, high levels of finished goods are sometimes part of a company’s strategy. An example of this is when retailers prepare for the busiest sales season of the year – between Thanksgiving and the Holidays.
Why Finished Goods Inventory Management Is Important
Efficient management of finished goods inventory can lead to reduced storage costs and minimize the chance of product spoilage and obsolescence. This is particularly important for perishable goods or products that have high storage costs.
Another reason why finished goods inventory management is paramount is that it leads to optimal sales and capital allocation. If the business has too much finished goods inventory, they have tied a large portion of capital in it. On the other hand, low levels of finished goods inventory means inability to meet customer demand and missed opportunities.
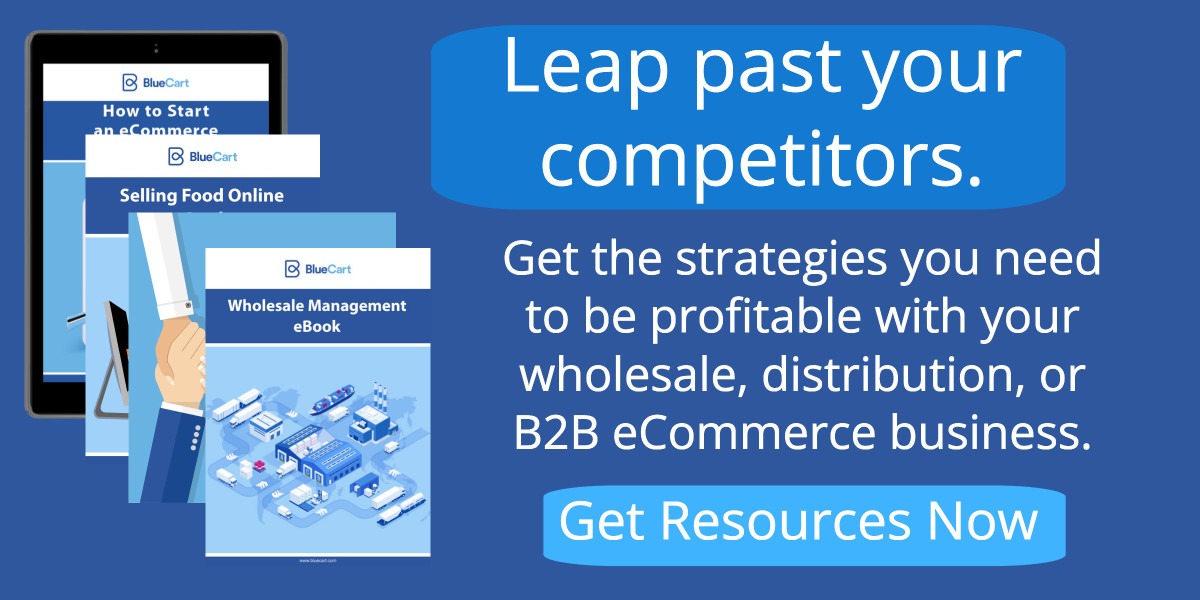
How to Calculate Finished Goods Inventory
There are two types of finished goods inventories: one at the beginning of an accounting period and one at the end. Whenever anyone speaks about calculating finished goods inventory, they’re talking about ending finished goods inventory.
How to find finished goods inventory requires three piece of information:
- Beginning inventory of finished goods
- Cost of goods manufactured (COGM)
- Cost of goods sold (COGS)
All three of these are used in the finished goods inventory formula.
How to Calculate Beginning Inventory of Finished Goods
How to calculate beginning inventory of finished goods is the same as calculating ending finished goods. You just did it last accounting period.
That’s because beginning inventory of finished goods is the ending finished goods inventory from last period. If you’re calculating finished goods inventory regularly, determining beginning inventory of finished goods is typically as easy as looking at your past balance sheet.
So, how do you calculate finished goods inventory? Let’s look into COGM first.
COGM Formula
The formula for cost of goods manufactured is:
Direct Raw Materials Used + Direct Labor Used + Manufacturing Overhead + Beginning WIP Inventory - Ending WIP Inventory
Where “direct” refers to raw materials inventory and labor that actually constitute or assemble the finished product.
COGS Finished Goods Inventory
Finished goods inventory has a big effect on the cost of goods sold (COGS). That’s because a manufacturer creates revenue when finished goods inventory is sold. Recognizing that revenue requires recognizing the COGS—because COGS considers the materials and labor costs applied to each unit sold.
Here’s a great resource for how to calculate COGS. And, long story short, here’s the formula:
COGS = Beginning Inventory + Received Inventory- Ending Inventory
Finished Goods Inventory Formula
The finished goods inventory formula is:
Finished Goods Inventory = Beginning Finished Goods Inventory + (COGM - COGS)
How Businesses Use the Finished Goods Inventory Formula
There are several reasons why businesses use this formula in their reports and when analyzing results. Let’s examine some of them.
- Thanks to calculating finished goods inventory, companies can avoid overproduction or stockouts. This metric is a crucial part of inventory management.
- Preparing income statements and other types of financial reports requires calculating a variety of important business metrics. Finished goods inventory is one of them.
- Thanks to the finished goods inventory formula, companies can plan future inventory needs and prepare according to their sales forecasting numbers.
- Calculating tax deductions related to COGS also requires using the finished goods inventory formula.
- A business might struggle if its sales volume is not aligned with production numbers. That’s why tracking production efficiency through the finished goods inventory formula is crucial.
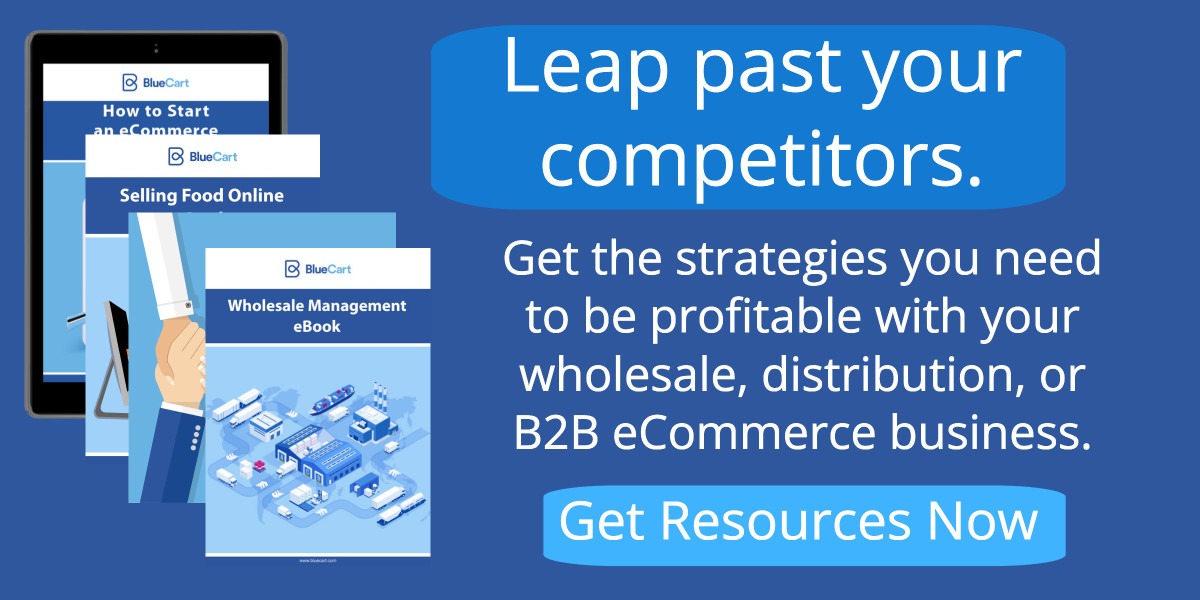
How to Get Finished Goods Inventory: An Example
Let’s say BlueCart Coffee Co. ended last period with $50,000 in finished goods inventory. That means this period their beginning finished goods inventory is $50,000.
Now let’s say their COGM for the period is $80,000 and their COGS is $60,000.
Here’s how to compute finished goods inventory:
Finished Goods Inventory = $50,000 + $80,000 - $60,000
Finished Goods Inventory = $70,000
And this $70,000 worth of finished goods inventory will, of course, be the next accounting period’s beginning finished goods inventory.
The Importance of Calculating Finished Goods Inventory
What’s the big idea? What’s the importance of calculating finished goods inventory?
- It identifies gross profit and current assets. Inventory is frequently a manufacturer’s largest profit driver and current asset. An accurate tally of current assets makes future operating budgets (like your MRO inventory spend) and financial budgets accurate.
- It helps keep waste down. If you know exactly what amount of inventory your business is capable of producing, you’ll make smarter raw materials purchases. You’ll also be able to tweak your safety stock levels and have less sitting inventory which frees up cash and lowers storage costs.
- It drives production efficiencies. You’ll be inventory tracking direct materials and labor costs. Looking over these historical numbers will allow you to tweak processes, integrate automation, and generally iterate toward cleaner, smoother inventory management. You may find that a just in time inventory setup or a vendor managed inventory agreement make sense after looking at the data.
Finished Goods Inventory Is Reported On The ...
Finished goods inventory is reported on the restaurant balance sheet as a current asset. That means they’re short-term assets meant to generate revenue within the next 12 months.
The manufacturing process, as outlined above, has multiple steps. All of these steps should be accounted for in inventory reporting. There is a raw materials account, a WIP inventory account, and a finished goods inventory account. When manufacturing is complete, the WIP account is credited and the finished goods inventory account is debited.
This way leadership and investors can accurately gauge inventory value by high-level insights into each inventory stage. That, importantly, gives them an idea of cash flow and how much cash is tied up in inventory. Two very important indicators of a company’s health.
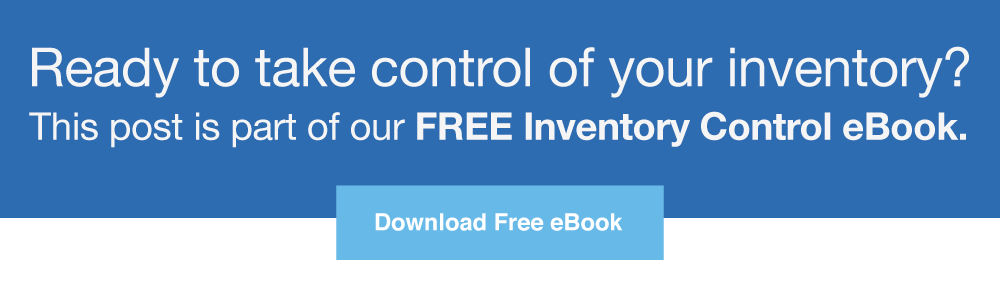
Finished Goods Inventory Turnover Rate
One big benefit of learning how to figure out finished goods inventory is that you can find your finished goods inventory turnover rate.
Finished goods inventory turnover rate is a ratio. It measures the rate at which a company’s finished goods inventory is sold and replaced (turned over) during a set time frame. Here’s how to find annual finished goods inventory turnover rate:
Finished Goods Inventory Turnover Rate = Annual COGS / Average Month-End Finished Goods Inventory Value
How to Calculate a Finished Goods Inventory Budget
A finished goods inventory budget considers the direct raw materials, direct labor, and overhead costs. In that sense, it’s similar to the COGM calculation, but it doesn’t take in account WIP inventory. All it’s doing is assigning a value to every unit produced based on raw materials, labor, and overhead. It’s not a cumulative indicator.
Calculating a finished goods inventory budget helps set profitable and competitive prices for the products being sold. Consider BlueCart Coffee Co. again.
Direct material: A cumulative $3 for green coffee bean and packaging material. That’s $3 per unit. Packaging can include eCommerce packaging.
Direct labor: Sorting, roasting, and packaging coffee beans wholesale takes about 30 minutes per bag. If a roaster makes $20 per hour, that’s $10 per unit.
Overhead: The roasting business has fixed overhead costs of $7 per hour and variable overhead costs of $2 per hour. That’s a total of $9 per hour overhead costs. The overhead costs per unit are then $9 times .5 hours, or the 30 minutes it takes to go from green coffee bean to packaged roasted bean. That’s $4.50 per unit.
Total individual cost: $17.50 per unit.
Total finished goods inventory cost: $17.50 x inventory volume.
Woof. That’s expensive coffee. But you get the point.
Management of Finished Goods Inventory
Management of finished goods inventory is important for companies of any size. That’s especially true if the company has multiple locations or more than one manufacturing facility. Finished goods inventory is usually managed and tracked with the help of ERP software. These powerful solutions allow businesses to accurately plan the sales of finished goods and decrease the risk of stockouts, excess inventory, or write-offs. Let’s examine the main features of finished goods inventory management software.
- Multi-location tracking and fulfillment. The power of these solutions is that data can be gathered quickly from multiple sources. That means excess shipping charges can be avoided thanks to more efficient fulfillment.
- Easier stock replenishment. ERP solutions use historical data to determine optimal par levels and replenishment dates. They calculate sales data, seasonality, number of inventory days, and average lead time to manage finished goods inventory reorders.
- Traceability. Managing finished goods inventory with the help of software will result in full traceability of every single item. This will make it easier for customers to track their orders. Furthermore, businesses can increase the efficiency of their fulfillment process or decide to switch fulfillment strategies altogether.
Outsourcing Management of Finished Goods Inventory
Using formulas to calculate finished goods inventory, managing stock, increasing inventory efficiency – a business can decide to outsource all these processes. Many 3PL (third-party logistics) companies offer a variety of services like fulfillment and inventory storage. That can be a cost-effective option for many companies, especially the ones in the eCommerce industry. Outsourcing management of finished goods inventory means you can focus on other aspects of the business such as marketing or sales. In addition, reputable 3PL providers give their customers the same benefits as an ERP solution – traceability, automation, demand forecasting, and many more.
So, What’s an Ideal Finished Goods Inventory Level?
It depends on your business. But, as a rule, you want to minimize finished goods inventory to keep storage costs down. What “minimize” means differs for each business. The point here is getting familiar enough with your finished goods inventory level that you can draw actually useful conclusions from it.
Like, how good are you at selling the things you make?
How much cash is tied up in your inventory, and how much could be freed?
Can you decrease the amount of pipeline inventory you have outstanding at any given time?
These are mega-important questions for both the B2B business model and B2C business model that can only be answered by sound finished goods inventory management. And once you have finished goods inventory numbers you’re confident in, you can start optimizing it. You can even start selling your products on an online marketplace with confidence.
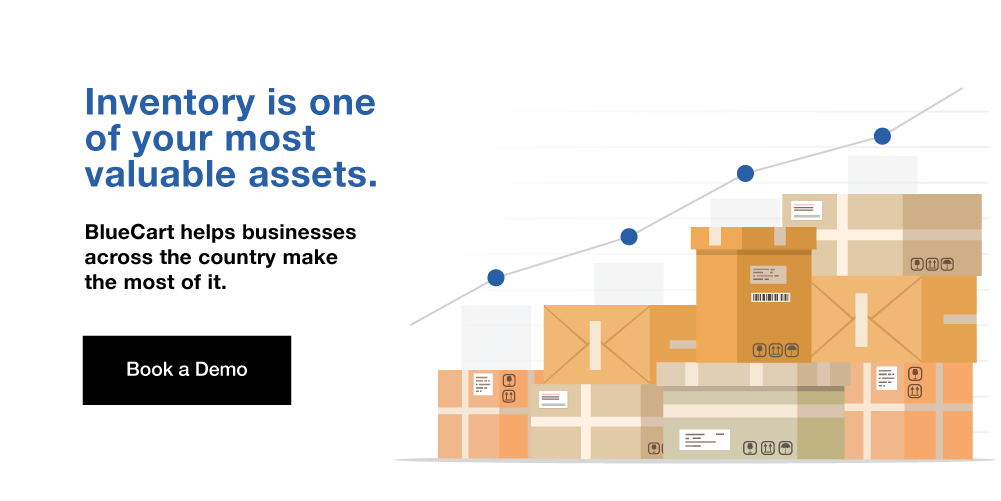
Frequently Asked Questions About Finished Goods
Turning raw materials into merchandise inventory is the essence of finished goods. But you also need to see finished goods in the context of your business’s financial health. Learn how to value finished goods with the commonly asked questions below:
What Is Beginning Finished Goods Inventory?
The term beginning inventory refers to the monetary value of items in stock at the start of an accounting period. Therefore, the beginning finished goods inventory of a company is the value of all the finished items (not counting raw materials and work-in-process inventory) the business has in its warehouse at the start of the accounting period. The beginning finished goods inventory is essential when determining production levels, calculating inventory turnover, and establishing the cost of goods sold (COGS). In most cases, the beginning inventory is the same as the ending inventory from the previous accounting period. For example, if a manufacturer of dairy products has $500,000 worth of finished goods (such as cheeses or packaged milk ready to be delivered) at the end of the year, that amount becomes the beginning finished goods inventory for the next year.
What Is Ending Finished Goods Inventory?
Ending inventory is the value of goods in stock at the end of an accounting period. Thus, the term ending finished goods inventory refers to the company’s stock of completed products that remain unsold at the end of the accounting period. This value is then carried over to become the beginning finished goods inventory for the next period. The ending finished goods inventory helps a company track its efficiency in sales and gives insight into production and marketing needs. Similarly to beginning finished goods inventory, the ending amount can help determine the optimal production levels, how to improve inventory turnover, and whether the cost of goods sold (COGS) is efficient.
How do you calculate finished goods on hand?
Finished goods on hand can be calculated with a simple formula. First, take your cost of goods manufactured (COGM) and subtract your cost of goods sold (COGS) from your COGM. Second, add your previous cycle’s finished goods inventory. The result is your finished goods inventory for your current cycle.
How are finished goods valued?
Finished goods are valued by taking your starting inventory, adding your cost of goods purchased or manufactured, and subtracting the cost of goods sold.
Let’s say your starting inventory is $3,481, your cost of goods manufactured is $5,000, and your cost of goods sold is $2,090. This gives you a finished goods value of $6,391.
What is the difference between finished goods and inventory?
The difference between finished goods and inventory is finished goods are ready for sale and shipment; inventory is any material or product that is used to make finished goods.
For example, let’s say your business makes soda cans. You order thousands of aluminum sheets with which to make the cans, which is considered raw materials inventory. It’s not until the sheets are put on a production line that they become work-in-process inventory, and when they’re made into cans, then they are finished goods inventory.
What are the example of finished goods inventory?
Examples of finished goods inventory include:
- Electronics like smartphones, laptops, and TVs
- Packaged food products such as canned wholesale seafood, wholesale snacks, and wholesale popcorn
- Clothing items like shirts, pants, and jackets
- Automobiles, motorcycles, and bicycles
- Furniture like chairs, tables, and sofas
- Cosmetics and personal care products like shampoo, soap, and makeup
What is a finished goods inventory?
Finished goods inventory refers to the stock of completed products that manufacturers have produced and are ready to be sold to customers, retailers, or other businesses. This type of inventory is the final stage of the manufacturing process, where the products are ready for wholesale distribution and wholesale sales.
How do you record finished goods inventory?
Recording finished goods inventory in eCommerce accounting typically involves the following steps:
- Track the quantity and cost of raw materials used in the production process
- Allocate labor and overhead costs associated with manufacturing the finished goods
- Calculate the total cost of goods manufactured (COGM)
- Add the beginning finished goods inventory to the cost of goods manufactured
- Subtract the cost of goods sold (COGS) during the accounting period
- The resulting value is the ending finished goods inventory, which should be recorded in the balance sheet as a current asset
Is finished goods the same as COGS?
Finished goods inventory and the cost of goods sold (COGS) are related but not the same. Finished goods inventory represents the stock of completed products that are ready to be sold, whereas COGS represents the total cost of producing and selling those goods during a specific accounting period. COGS is an income statement item that helps businesses determine their gross profit, while finished goods inventory is a balance sheet item that represents the value of completed products held by the company.
Do Service Companies Track Finished Goods Inventory?
It’s uncommon for service-oriented businesses to track finished goods inventory. It’s a metric that’s closely associated with the manufacturing of goods. In some cases, companies that are service-oriented might also manufacture certain goods. For example, a company that specializes in providing gardening and landscaping services might also grow certain plants or other greenery. In that case, the company might track raw materials and work-in-progress (WIP) inventory as well.
How Is Finished Goods Inventory Stored?
Storage of finished goods depends on their type. For example, food products might need to be stored in a controlled environment at low temperatures. On the other hand, apparel and clothing products should be stored away from sunlight, as it can affect their colors. Generally speaking, storage of raw materials, work-in-progress inventory, and finished goods depends on the type of product. Proper storage conditions can ensure the longevity of inventory and compliance with regulations.
Are There Different Types of Finished Goods Inventory?
Yes, there are. Finished goods inventory is a broad category that can be broken down into other subcategories. Not all companies do that but when sales increase, it’s important to have proper business processes to answer the increased demand. Implementing the following subcategories of finished goods might be a good starting point in that regard.
- Ready for sale. As the name implies, these are products that have been manufactured and await to be sold. These products can be packed and shipped at any desired moment.
- Allocated. This subcategory of finished goods inventory is for items that have been purchased by a customer but are not yet shipped. They are removed from the ‘ready for sale’ inventory as they cannot be sold again.
- In-transit inventory. This refers to products that are being moved to another warehouse or are shipped to the customer.
When it comes to finished goods inventory, some companies have adopted other categories as well. For example, items that have stayed for too long in inventory might need maintenance or repair and can be separated in different subcategory. Here are a few additional examples.
- Seasonal stock. Before periods of high demand, manufacturers might produce more items anticipating the surge in interest. Good examples of periods when seasonal stock is produced are Black Friday and the holiday season.
- Safety inventory. If your business has experienced supply chain disruptions or anticipates an upturn in demand, having additional finished goods can be a good idea. These products can be in a separate inventory category or warehouse and be used in case the forecast of an increased search materializes.
How do we classify finished goods?
Finished goods are typically classified based on their type, purpose, or industry. Some common classifications include:
- Consumer goods: Products intended for direct use or consumption by end customers, such as wholesale microgreens seeds, gourmet popcorn, and wholesale dairy
- Industrial goods: Products used by businesses for further production, such as machinery, microgreens kit, bakery equipment, gourmet popcorn business equipment, and raw materials
- Durable goods: Products with a long useful life, such as automobiles, appliances, and furniture
- Non-durable goods: Products with a short useful life or that are consumed quickly, such as wholesale alcohol, seafood subscription box and disposable items