As a business owner, you may struggle to know exactly how much product you should have on hand. Due to this, many businesses find themselves closing their doors as they wait for their much-needed supplies. However, with material requirements planning (MRP), you won’t run into such a problem.
Now you may be wondering “What is MRP?”, and how it helps businesses determine how much product they need. Material requirements planning software is used by businesses to stay on top of inventory control. In fact, with such software, you can also avoid ending up with too much product.
This article covers exactly what is MRP. It also dives deep into how material requirements planning software will allow you to meet customer demand while controlling your inventory.
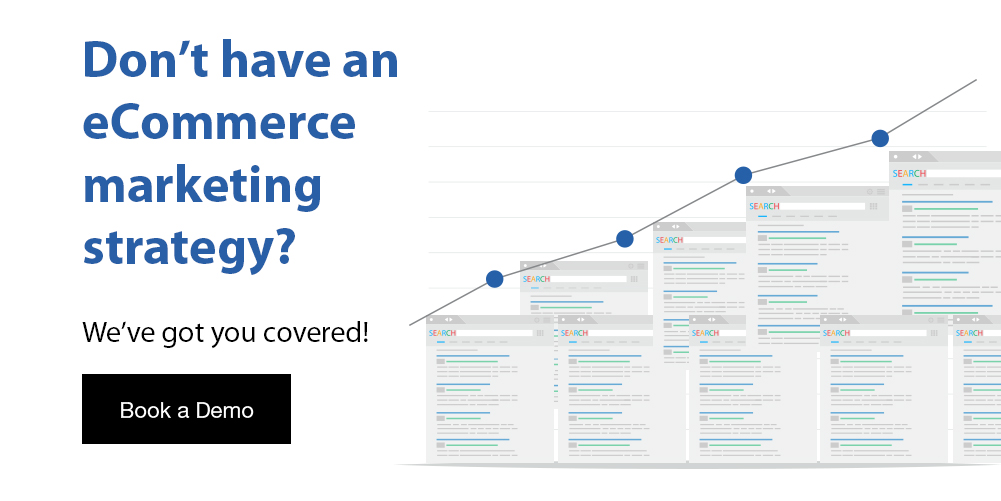
What Is MRP or Material Requirements Planning?
MRP stands for material requirements planning, and it’s a manufacturing process that is used by businesses to plan and control the supply chain. This includes the food and agricultural supply chain.
If you’re still asking yourself, “what is MRP?”, keep in mind that MRP converts the manufacturing plan into a specific timetable. This means that you can order raw materials and products. Familiarize yourself with what is raw materials inventory to better understand what’s included.
It’s common for manufacturing companies to use MRP to forecast consumer demand for specific items. This is especially true for high demand products. The forecasting process includes predicting the type and amount of goods they will purchase as well as the materials required to manufacture the product.
Material requirements planning software is often used along with other systems. These include enterprise resource planning (ERP) and supply chain management (SCM) systems.
Businesses rely on MRP software as it addresses different issues that manufacturers run into on a daily basis. These include the scheduled production requirements, delivery of raw materials, and overall inventory control. It’s also possible for material requirements planning software to use analytics to determine when extra suppliers are needed and place orders automatically.
How Does MRP Work?
Material requirements planning or MRP works by tracking business activity and interacting with the planning and scheduling systems to ensure everything is running smoothly. This allows businesses to focus on the order fulfillment process for customers while ensuring customer satisfaction.
The three steps in the MRP process include:
- Identify what products need to be produced. The bill of materials (BOM) will include information on what materials are used for each product. Businesses will use the BOM to identify the exact materials that are required, which parts are dependent on others, and how many products need to be produced.
- Quantify the demand for those products. Material requirements planning software will calculate the quantity for the final products that are required in order to meet demand. This is based on the customer orders and forecast analytics from the sales department. It also excludes the on-hand inventory.
- Determine the supply. MRP software uses the bill of materials and master production schedule (MPS) to calculate the components, assemblies, and materials that require production or purchase. It also checks the inventory on-hand to determine if there are any net shortages. Then, it determines the ideal quantity for each item that must be purchased or produced.
Types of Data in Materials Requirement Planning (MRP)
Material requirement planning software synchronizes the flow of various components and materials in the business and production process. During this process, it filters through parameters such as:
- Sales orders
- Expedited orders
- Purchase orders
- Due dates
- Order forecasts
- Materials shortages
- In-store and online marketplace demand
- Inventory cost
- Materials
- Data
- Capacity
- Shelf life
- Production scheduling
- Bills of material
- Inventory levels
Key Takeaway: Businesses use MRP or material requirements planning software to manage the materials used in the production or manufacturing process.
The Importance of MRP
Material requirements planning is done using specific software that ensures the right inventory amounts are available for production. This speeds up production time and focuses on producing at the lowest possible cost. Costs include the inventory carrying cost and manufacturing inventory costs.
Businesses that use MRP, improve the flexibility, profitability, and efficiency of their manufacturing operations. In turn, companies improve their product quality, factory workers improve their productivity, and there’s an opportunity to minimize material and labor cost.
The proper use of material requirements planning software allows manufacturers to quickly respond to any increase in demand for their products. It also avoids inventory stock outs and production delays thanks to the wholesale inventory management functions. This contributes to business stability and revenue growth. MRP is constantly used in the business industry, especially when it comes to wholesale business software.
Pros of Using MRP
Just like with all efficient business systems, there are pros and cons to using material requirements planning software.
The pros to using MRP software include:
- Reduction in inventory costs
- Improved manufacturing efficiency
- Reduced lead time
- Enhanced labor productivity
- Consistent material and component availability
- Effective inventory management process
- Competitive product pricing
- Reduced inventory levels and associated costs
Cons of Using MRP
Be sure to consider the cons of using material requirements planning software. However, be aware that the pros of MRP software typically outweigh the cons for most businesses.
The cons of using MRP software include:
- Production scheduling flexibility will be reduced
- MRP software may be expensive and difficult to implement
- Data integrity requirements must be followed
- Must pay attention to data input accuracy
What Is ERP vs MRP
Businesses use many systems to ensure the efficiency of their company. Some of these systems streamline business operations. This includes material requirements planning (MRP) and enterprise resource planning (ERP). Familiarize yourself with the ERP meaning.
Some might confuse ERP and MRP, the two systems are quite different. However, MRP is a component of ERP and ERP originally came from MRP.
The evolution of material requirements planning software started with integrating different modules including purchasing, inventory, bills of materials, and production control. These were then combined with accounting and finance functions to create MRP II.
MRP II continued to evolve and incorporate new capabilities. The term to describe these new and broad functions turned out to be enterprise resource planning or ERP software.
ERPs stand out from MRP because enterprise resource planning systems allow businesses to plan and automate various back of house business processes. MRP systems, on the other hand, allow businesses to focus on materials' management. ERP is ideal for manufacturing, accounting, quality, customer management, supply chain, processes, and planning.
To better understand enterprise resource planning and the benefits of ERP, look into ERP wholesale and ERP examples. You may also want to look into the best ERP systems and ERP implementation options for your business. Now, ERP and MRP can be integrated with wholesale ordering software.
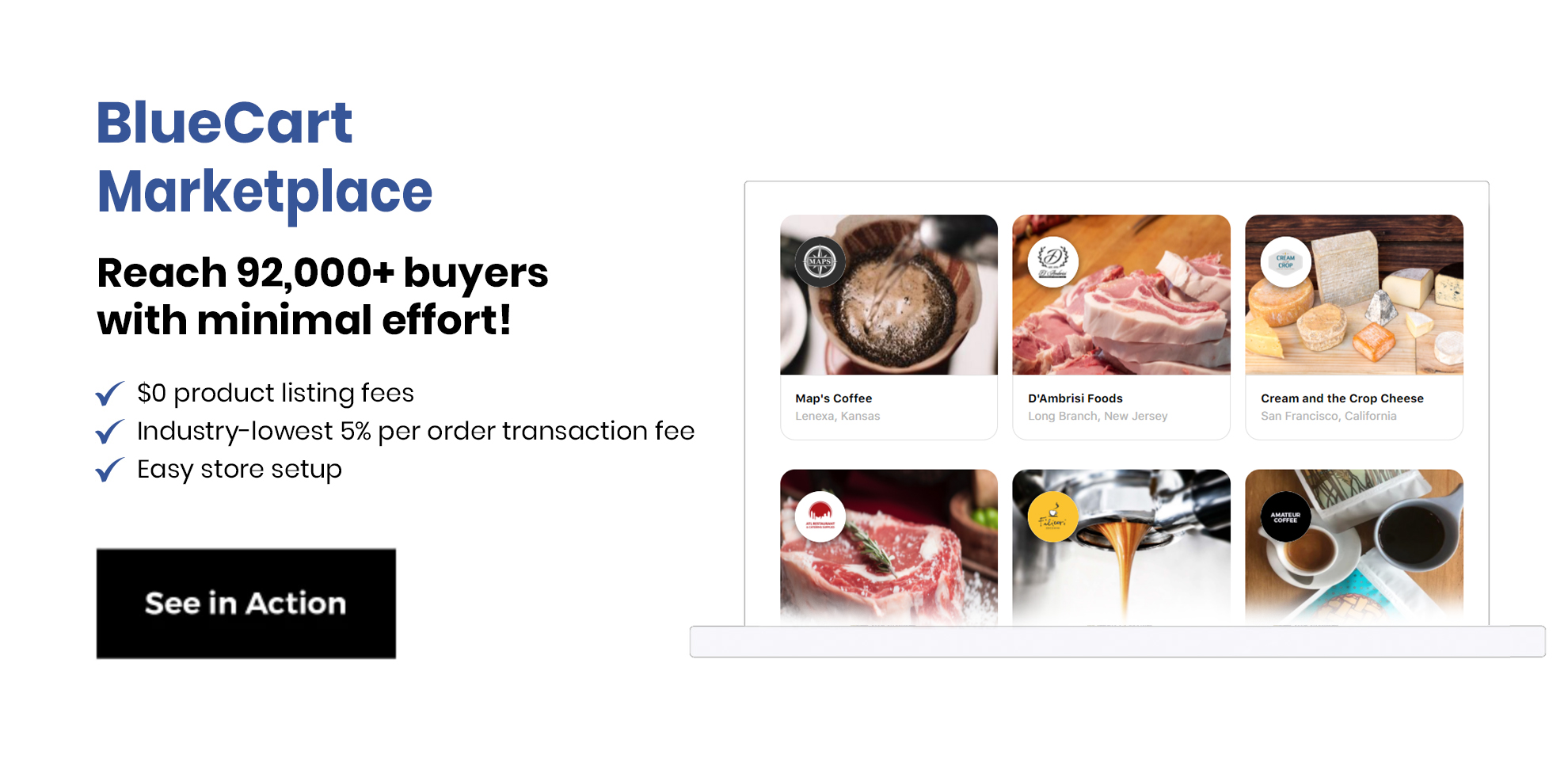
Frequently Asked Questions About Material Requirements Planning and What Is MRP
This article should have answered your question, “What is MRP?” If you still want to know more about material requirements planning, read the following questions and answers. They cover topics regarding, “What is MRP?” and how it differs from other business systems.
What Is the MRP Definition?
Material requirements planning or MRP refers to a system that allows manufacturers efficiently to manage, plan, and control their inventory. This schedules the manufacturing process based on the bills of materials. As a result, manufacturers deliver the right product amounts at the right time and for the lowest price possible.
What Is the Difference Between MRP and ERP?
The main difference between MRP and ERP is that MRP refers to materials management, whereas ERP allows businesses to plan and automate their back-of-house business processes. ERP systems allow companies to focus on manufacturing, customer management, accounting, processes, planning, supply chain, and quality.
Is MRP a Software?
Material requirements planning, or MRP, is software that allows manufacturers to schedule, plan, and control the materials that are used in the manufacturing process. Some businesses rely solely on ERP software, as it contains some MRP functions.