The common understanding is that inventory refers to things you have. Not things that are floating across the Atlantic Ocean. That’s why, sometimes, pipeline inventory and in transit inventory are overlooked (see what is inventory).
But your inventory is your inventory, no matter if it’s in your hand or on an international freighter. And your inventory is one of your company’s biggest assets. Which means a sharp inventory management process (like vendor managed inventory) and accurate inventory accounting immediately increase the financial health of your business. It can even be useful to have a shipping cost estimator to stay on top of costs.
Here's what pipeline inventory and in transit inventory are. Along with an explanation of decoupling inventory and how it helps mitigate some pipeline risk. We’ll cover all the shipping terms you need to know to understand how pipeline inventory and decoupling inventory will affect you and your business.
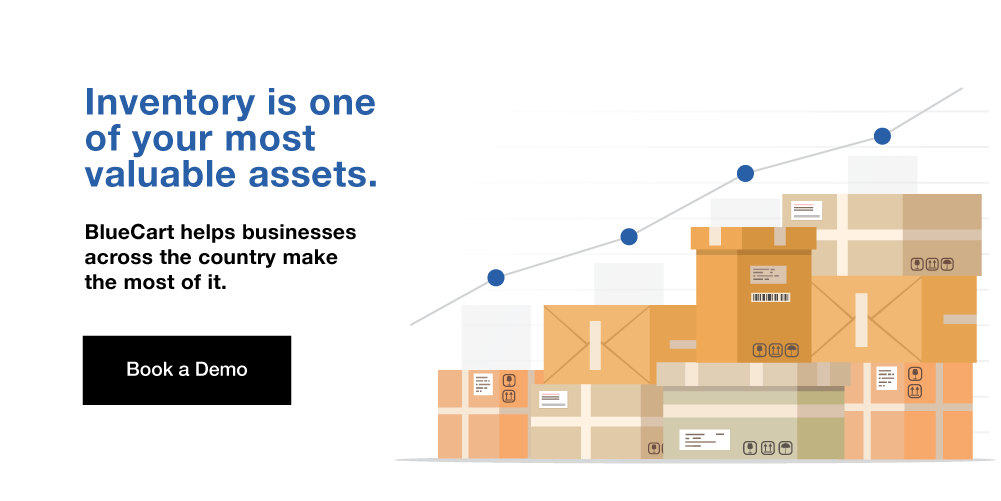
Pipeline Inventory: What Is It?
First to define pipeline inventory. Pipeline inventory is all the items that are in-transit between the different locations of a supply chain. Maybe the inventory is on its way to a factory from a large distributor, where it will turn into finished goods inventory. Or it may be on its way from a factory to a retailer to become merchandise inventory. Point is, all pipeline inventory has yet to reach its final destination. A pipeline inventory example could be anything currently in transit.
Pipeline stock shows up commonly in two contexts:
- Manufacturing operations that oversee supply chains with numerous factories and suppliers; especially complicated supply chains that involve overseas shipment
- Retail companies with physical locations that receive inventory from warehouses-where a warehouse management system might come in handy
The bigger a company is, the more pipeline inventory it has, and the more important it is to track it accurately. It can be one of the trickier types of inventory. It's nothing as simple as cycle stock. So we wouldn’t dare define pipeline inventory without an example. Here ya go. You can use this when you need a pipeline inventory calculation to check in with.
Pipeline Inventory Example
There are some situations where it takes weeks or months for inventory to change hands. Overseas freight shipments, particularly. Think of a shipment of automotive parts from Germany that takes a month to arrive to a car manufacturer.
These items are considered part of the shipper’s inventory during their transit—up until the buyer pays for them. Once that buyer (in this case, the car manufacturer) pays for them, they’re considered part of that manufacturer’s inventory. The movement of that inventory is documented in the process of when they record a sale, and when their stock refers to a specific shipment and location. Stock levels can vary in slight degrees as inventory is in transit.
Decoupling Inventory
Decoupling inventory is any inventory set aside to meet purchase orders in the case of inventory production slowing or stopping-it could even help at a time when a backorder issue shows up. That makes decoupling inventory a type of safety stock not pipeline inventory. Decoupling stock is often grouped with pipeline inventory, but pipeline inventory refers to its own specific situation in the stock chain. They're both completely different from the deadstock meaning.
In Transit Inventory: Transit Inventory Definition
In transit inventory, also called transportation inventory or goods in transit, is any product shipped by a seller but not yet received by a buyer. It’s similar to pipeline inventory, almost identical. But it’s a term primarily used by the company that’s selling and shipping the product. It’s another way of looking at a work in progress shipping order.
The main consideration shippers must make with in transit inventory is when the ownership of the inventory changes hands, on paper, to the buyer. AKA, the buyer officially buys it. That can happen either:
- When the inventory is loaded onto the freight vessel for shipment, AKA freight-on-board shipping point, or
- When the inventory arrives at the purchaser, AKA freight-on-board destination
The exchange of money and, thus, inventory happens at one of the two depending on the contract between buyer and seller.
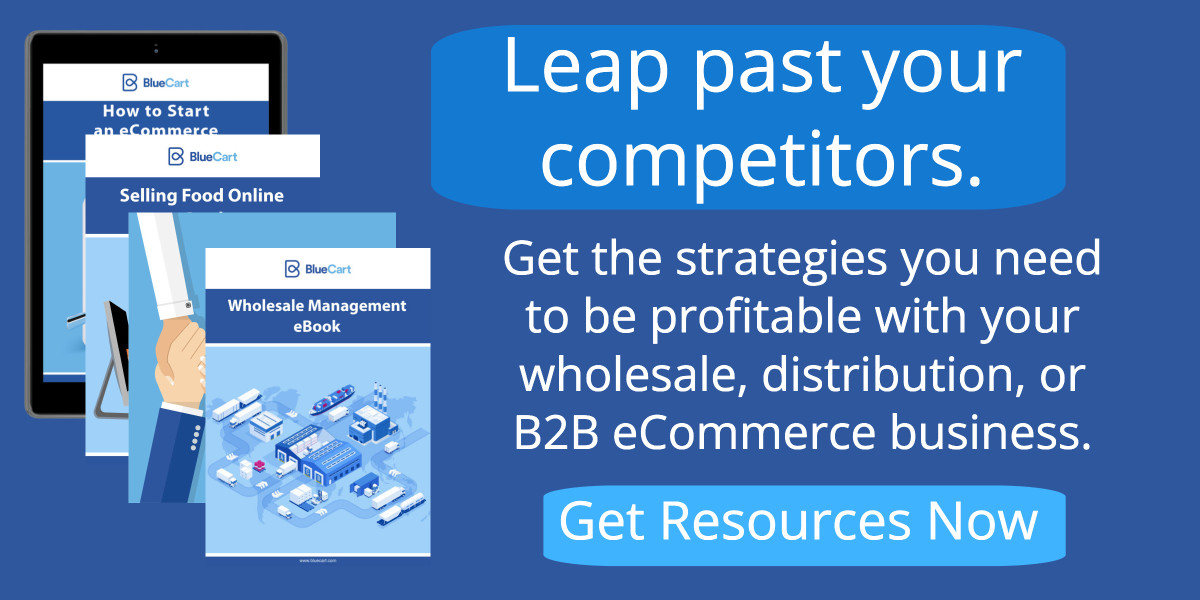
Goods In Transit Are Included In a Purchaser’s Inventory
Goods in transit are included in a purchaser’s inventory, even if they are not in physical possession of the items, when those items have been paid for.
Calculating Pipeline Stock In Inventory Management
Managing pipeline inventory successfully depends on calculating it accurately. Here’s the why and the how.
Why Bother with Pipeline Inventory Calculation?
Calculating pipeline inventory is crucial to figuring out how much cash is tied up in inventory—and other overheads like transportation and carrying costs. And it’s particularly important for businesses with long lead times. Inventory is a valuable asset, and businesses that have lots of cash tied up in it must see that their balance sheet reflects it.
Only then will you, your board, your investors, and leadership get an accurate picture of your company’s cash flow.
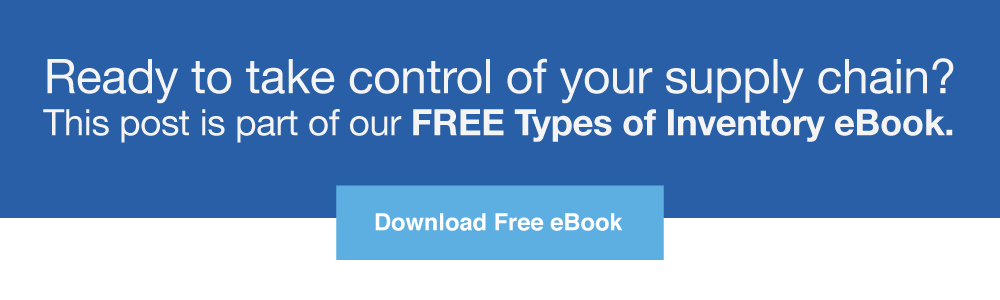
How to Calculate Pipeline Inventory
The pipeline inventory formula is:
Pipeline Inventory = Lead Time X Demand Rate
Here’s an example. Consider the fictional BlueCart Coffee Co. When they order green coffee beans from their grower across the world, it takes 3 weeks (lead time) for those beans to arrive. Each weekly order they place is for $5,000 worth of green coffee beans.
Pipeline Inventory = 3 X $5,000
Pipeline Inventory = $15,000
At any given moment, BlueCart Coffee Co. has $15,000 in pipeline inventory. This is important to know when finalizing end-of-period balance sheets and tallying up your raw materials inventory, work in process inventory, MRO inventory, and finished goods inventory. You’ll only have a true picture of your inventory’s equity if you include pipeline inventory in the mix.

Optimizing Pipeline Stock In Inventory Management
There are two tried-and-true ways to get into optimizing pipeline stock in inventory management. Shipping contingencies and calculating EOQ.
Shipping Contingencies
Pipeline inventory is in a bit of a gray area. It may be paid for and officially on the buyer’s balance sheet. But if shipping issues arise during transit, buyers must rely on a third party to solve the problem.
In situations where goods in transit are slow-moving, lost, late, or not built to spec, have solid contingency plans. Decide when to discount or liquidate stock. Have a plan in case deliveries are way late (hello, decoupling inventory), etc. Be prepared.
Calculate the Economic Order Quantity (EOQ)
EOQ is a formula buyers use to zero-in on just the right amount of inventory to buy. It minimizes carrying and inventory costs. That means less pipeline inventory, less risk, and less decoupling inventory. Here’s the formula:
EOQ = √͞ ((2 X Demand X Ordering Costs) / Carrying Costs)
Demand is the units ordered from your business in an accounting period. Ordering costs are how much the item costs you to acquire or produce. Carrying costs are how much it costs to store the item.
Back to BlueCart Coffee Co. Each bag of roasted coffee beans costs $8 to source, roast, and package. You sell 1,000 bags over the accounting period in question, and it costs 10 cents to store it.
EOQ = √͞ ((2 X 1,000 X 8) / .1)
EOQ = √͞ (160,000)
For the next accounting period, the ideal order based on these figures is 400.
Pipeline Inventory Is Special
It’s special because it’s not like the other inventories. It’s far away from home and needs extra love and support.
That’s why all good pipeline inventory management involves contingency planning and decoupling inventory stock. Some use the EOQ method, too, though there are numerous other inventory forecasting and purchasing models out there to help with buyer strategy.
One great way to streamline procurement and boost profits is a 360-degree digital wholesale marketplace and eCommerce platform like BlueCart. It helps you streamline your communication, processes, and payments so you don’t get into inventory quagmires in the first place.
Frequently Asked Questions About Pipeline Inventory
Now that you’re familiar with pipeline inventory as a whole, it’s easier to know how to calculate and use it. We compiled some frequently asked questions and answers about pipeline inventory below.
What is a pipeline supply chain?
A pipeline in any supply chain refers to the processes materials go through before they reach the buyer and are ready for assembly or manufacturing. The fewer materials needed for a product, the less complex the supply chain; the more materials needed, the more complex.
Pipeline inventory refers to supplies that have been ordered but haven’t arrived at a warehousing or manufacturing facility yet. It’s important to order new stock with enough lead time to allow products to be shelved, manufactured, and shipped without delays.
What is the average pipeline inventory?
Your average pipeline inventory depends on how many units you request per order and the length of lead time required for the products. Since every industry and supplier is different, it’s impossible to standardize pipeline inventory across businesses.
However, you can use this formula to determine your own average pipeline inventory:
Number of units ordered per week x Lead time for the product in weeks = average pipeline inventory.
If you order 1,000 units per week and there is a two week lead time for that product, your pipeline inventory will be 2,000.
What is the in transit inventory cost?
In-transit inventory cost refers to how valuable pipeline inventory is to your business and the expenses associated with it. Inventory costs go beyond just the price of buying materials; it costs you to ship and store them, too.
Calculating your business’s in-transit inventory cost is much easier with the right formula. Here’s how to do it:
- Step 1: Average shipment value x annual inventory carrying cost / 365 = daily carrying cost
- Step 2: Daily carrying cost x number of days in transit = average shipping container cost
- Step 3: Average shipping container cost x number of containers shipped = average in-transit inventory cost
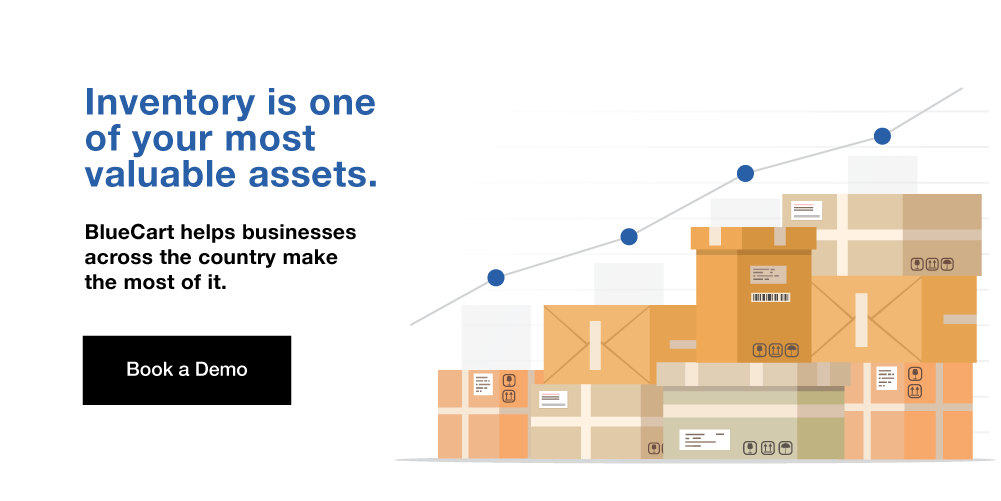
Pipeline Inventory: Send It Down the Pipes!
For anyone in the shipping and selling industry, a firm understanding of pipeline inventory, in transit inventory, and everything in between–pardon the pun–will be helpful in feeling secure in shipping terms. The world of shipping can be rocky, but a solid understanding of terminology and different situations can keep you steady. The BlueCart blog is always here to help you learn more. We can also help you learn about everything from dropshipping to eCommerce, and from dairy shipping to wholesale meat. Wherever you're at in the food supply chain, we've got you covered.