Managing, analyzing, and optimizing inventory is a never-ending job and often defines the success of a direct to consumer or B2B business (see what is a B2B company). It’s arguably the most important thing to get right if you want your business to grow. You’ll often find the inventory definition accounting for a good amount of the information on inventory you’ll find online, because it’s a definition with a wide range. While inventory itself starts as a simple topic, the deeper you go, the more there is to learn depending on your business type, and how involved you want to be in your inventory process.
That’s why there are so many concepts around inventory you should understand such as the inventory days formula. There are a lot of ways to look at inventory’s effects on operation and profitability. Let’s run through the big ones to flesh out the ripple effect inventory has across your business. After this article, you’ll have a finger on the pulse of your inventory, and your inventory and business management will be all the better for it.
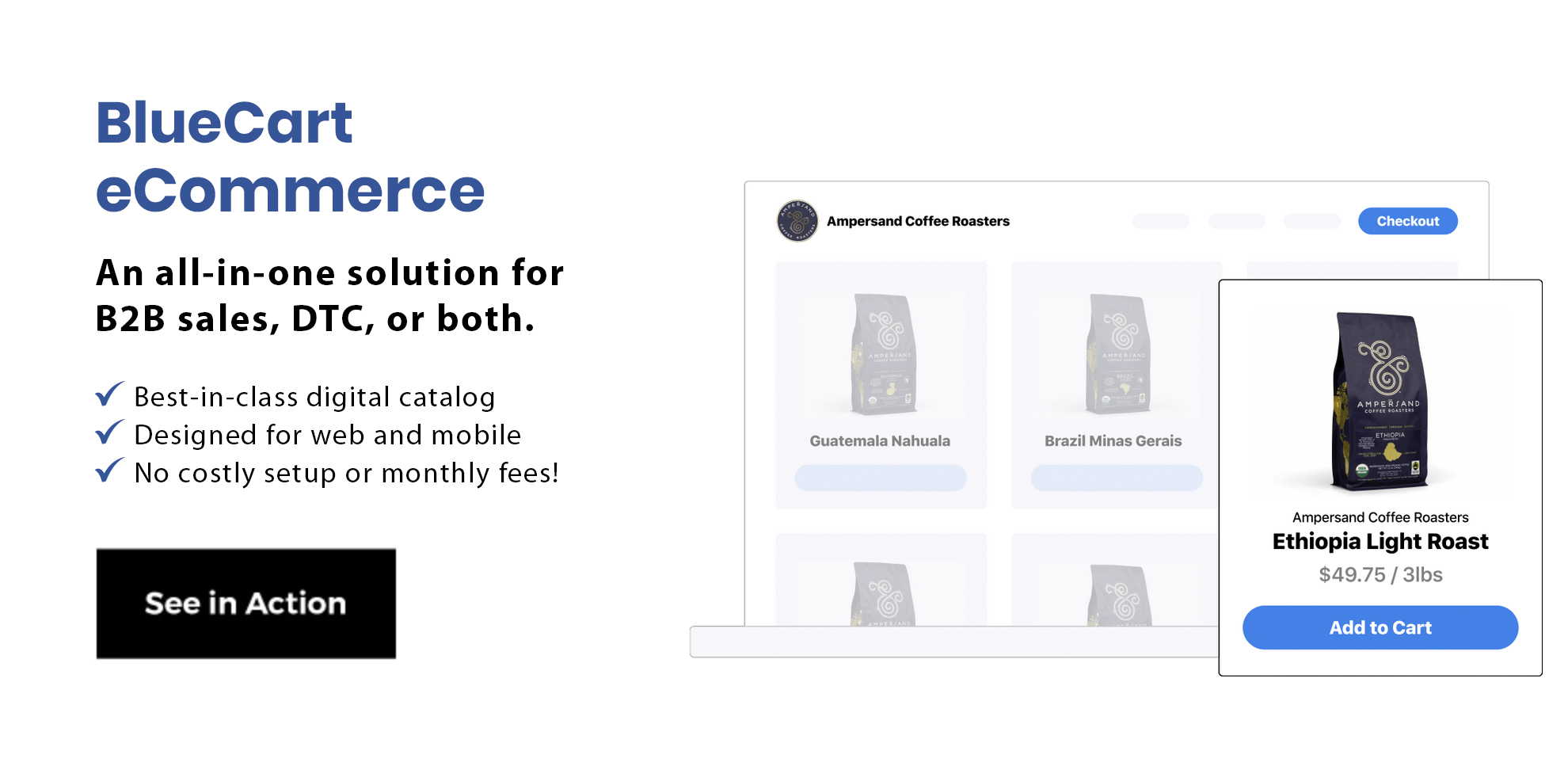
Inventory Meaning: What Does Inventory Mean?
Inventory, in business, is all the goods that a company owns, produces, and uses in service of production at any given time. It’s typically physical goods, though it can refer to services, like all work done prior to the sale. It’s usually a company’s largest current asset, or an asset expected to sell within the year.
That’s the general definition. And there are many types of inventory to consider within that definition.
But beyond that inventory meaning, there are a host of other related concepts whose definition will provide useful context to an understanding of inventory.
Let’s consider some.
Inventory Definition Accounting
Inventory is listed on a company’s balance sheet as an asset. That’s why the inventory definition from an accounting perspective takes into account the specific phases of production. Because inventory’s value is recorded and reconciled based on its place in the production pipeline.
Inventory, in that sense, is all the raw materials inventory, work in process inventory, decoupling inventory, and finished goods inventory that a company acquires and produces. Each of those types of manufacturing inventory can be recorded on the balance sheet separately. That’s why it’s a particularly apt inventory definition from an accounting angle. It even ties into the cost of goods sold, as your inventory definition accounting needs are closely tied to the cost of running your business.
Inventory Definition Economics
From a general economics perspective, inventory is all assets held by a business with the intention of selling in the market for profit.
Inventory levels and reactions to market consumption can have a broad economic impact. If, for example, consumption of inventory in the market declines, any investment in inventory results in an accumulation of unsold goods.
Sitting inventory ties up cash and costs money to store. In large enough quantities—with enough decline in demand—inventory issues can cause widespread and substantial issues to entire industries.
Inventory Management Definition
Inventory management is the process of buying, storing, using, packaging, and shipping inventory. It covers the warehousing and processing of all goods that a business uses in production and produces.
A simple way to look at inventory management techniques is as the balancing act between excess inventory and having to wait on an order (read more on backorder meaning) profitable items. This can be achieved by using the average inventory formula.
Shortages and excesses can indicate problems in inventory forecasting, production efficiency, and raw material acquisition. And they can have a big impact on a business’s bottom line. To thread the needle of optimal inventory operations, companies rely on inventory management to hit their inventory management KPI.
Quality inventory management can help in all aspects of your business. From better quality control to warehouse management to the success of your final product, having an inventory management system that suits your needs is crucial. Inventory control systems can take any business from good to great. It can increase your lead times, help you have more precise inventory tracking, and get you ready for sale items to fly off your menu and your shelves.
Inventory Turnover Definition
Inventory turnover is the ratio at which a company can turn goods into cash. It’s also called inventory turnover ratio, for obvious reasons. It’s an important factor when appraising a company’s financial health.
Why is that?
Well, the inventory turnover definition can be put another way. It’s how many times a company has sold and replaced their inventory over a specific period of time.
For most companies, this is their sole purpose. To create and sell a product. Inventory turnover, then, is a convenient metric that indicates just how good a company is at doing that. Inventory turnover also ties into the interest inventory definition. Interest inventory is an inventory check of how customers are reacting to your products and services. If you own a restaurant, taking an interest inventory could involve tracking the sales of a specific menu item for a month, to see how many people purchase it. You could also keep note of those customers who do purchase it, and see if they order it again, leave a review online, or anything else to show how they enjoyed it. Basically, you’re taking an inventory of their interests to keep your inventory focused on the products people want.
Let’s say a coffee company’s monthly inventory turnover rate is 6 for their decaf blend. That means that over the course of a month, they sell and replace their entire decaf blend inventory 6 times.
Most companies end up with an inventory turnover rate of between 5 and 10. The higher the better.
Inventory turnover ratio is also called inventory turns. Any inventory turns definition will cover the same information above. Calculating turnover is easy with the inventory turnover formula.
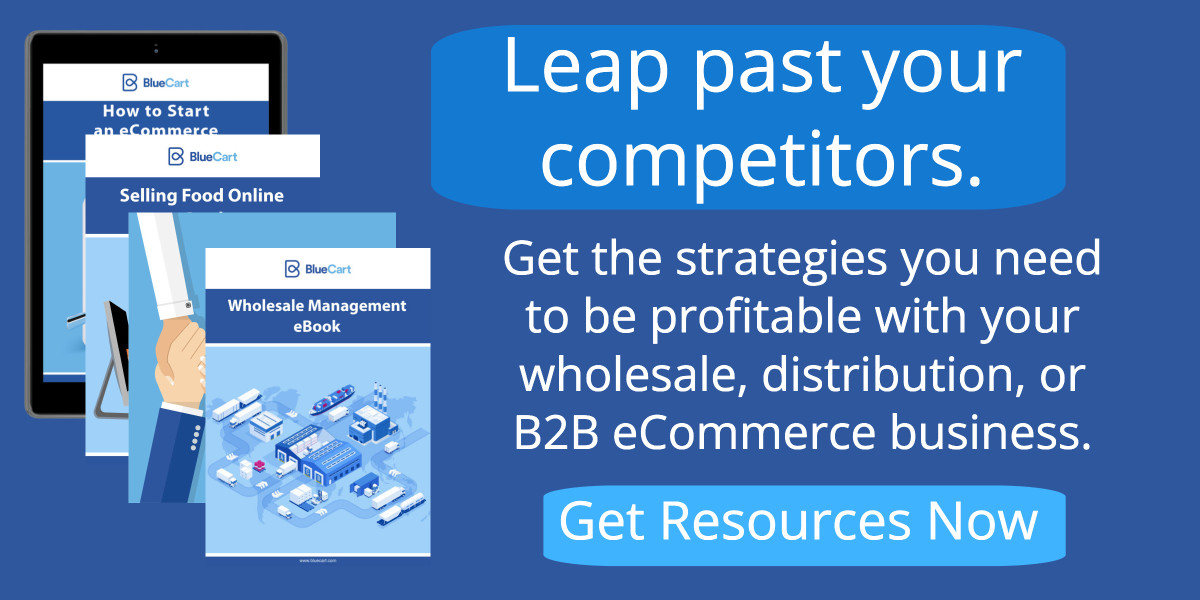
Inventory Control Definition
Inventory control is the regulation of the inventory a company has on-hand to ensure optimal inventory production. Tight inventory control means the right amount of safety stock to avoid overstock and shortages.
It differs from inventory management with respect to scope. Inventory control focuses on maintaining and adjusting inventory levels to ensure the most efficient production possible. Inventory management, on the other hand, is higher-level management of inventory. It includes which suppliers to work with, shipping routes, demand forecasting, etc. Inventory control is a part of inventory management.
Perpetual Inventory Definition
Perpetual inventory is a way to account for inventory that immediately records the purchase or sale of inventory. It then immediately adjusts the total inventory numbers accordingly. This is done with inventory management software that records all transactions and an inventory database that is adjusted based on those transactions.
In other words, it’s an inventory accounting method that happens automatically because software makes our lives easier.
As long as a company has inventory management software integrated into a POS system, every movement of inventory is recorded and cataloged in the database. Nothing enters the inventory pipeline without immediately being added to the database. And nothing exits without immediately being removed.
That way your inventory database always accurately reflects your current inventory levels and is adjusted in real time. And it can be done in your own facility or with vendor managed inventory.
A perpetual inventory system is opposed to a periodic inventory system. A periodic inventory system maintains records of its inventory by regularly scheduled physical counts of inventory.
Perpetual Inventory System Definition
A perpetual inventory system is opposed to a periodic inventory system. In a periodic inventory system a company tallies up their inventory stocks every once in a while. Or periodically. Then they compare a current number against a previous number to determine inventory change over time. They're also a vital form of eCommerce shipping software.
But in a perpetual inventory system, inventory levels are monitored in real time. And all inventory management and control decisions can be made at any time based on current, accurate numbers. Because those numbers are all updated perpetually, after every purchase and every sale. A perpetual inventory system is like a consistent ABC analysis that helps you stay on top of your inventory, track your reorder points in real time, and never have to wonder how accurate your inventory reports are.
Inventory Synonym: Another Word for Inventory
There are some other ways to refer to the goods a company has on-hand. Here are some inventory synonyms:
- Stock
- Supply
- Reserve
- Store
- Cache
- Stockpile
- List
- Record
- Account
- Catalog
Inventory vs Stock: Is Stock the Same as Inventory?
Stock is what’s sold by a business, perhaps through a wholesale marketplace. The merchandise inventory, in other words. Stock doesn’t include the goods and materials required to produce finished products. That’s what inventory is: all the materials required to produce finished goods, along with the finished goods themselves. In other words, inventory and stock control and management are two sides of the same coin, with a few similarities on each side, but different values to the company overall.
Inventory can be managed through the use of an ERP accounting system. Learn about the benefits of ERP to understand how it's possible. It's also possible to use a SKU number to manage inventory.
Inventory vs Supplies
Supplies are a type of inventory. Supplies, or supply inventory, is usually another name for MRO inventory. It’s composed of the consumable materials, equipment, and supplies that are used for production but aren’t a part of the finished product.
Examples include personal protective equipment, cleaning supplies, office supplies, tooling and industrial equipment, and more.
Frequently Asked Questions About Inventory Definition
The inventory definition covers so much ground, and there’s always more to learn. Our answers to these frequently asked questions will pique your curiosity and get you on track to keep exploring the inventory definition and how it relates to your business.
How Do You Spell Inventory?
Here’s how to spell inventory:
INVENTORY.
That’s not to be confused with the plural inventories.
Remember, a y for singular, and ies for plural.
What is the Inventory Pronunciation?
The phonetic American pronunciation of inventory is IN-ven-taw-ree. The accent is on the first syllable.
The phonetic British and Australian pronunciation is IN-ven-tree. The accent is also on the first syllable.
How Do I Use Inventory in a Sentence?
Here’s a few ways to use inventory in a sentence:
As a noun:
We counted the bar’s inventory using a bar inventory spreadsheet after last call.
The inventory was shockingly low after the sale.
Pipeline inventory refers to inventory currently in transit between two parts of the inventory pipeline.
As a verb:
We inventoried all the books in the library.
What Are the Different Types of Inventory?
The main types of inventory include:
- Raw Materials: Basic components used to produce goods.
- Work-in-Progress (WIP): Items that are in the process of being manufactured.
- Finished Goods: Completed products ready for sale.
- Maintenance, Repair, and Operations (MRO): Supplies used in the production process but not part of the final product.
- Safety Stock: Extra inventory kept to prevent stockouts
What Is an Inventory Audit?
An inventory audit is a process of verifying the accuracy and completeness of inventory records. It involves physical counts of inventory, reconciling discrepancies, and ensuring that inventory valuation methods are correctly applied. Regular audits help identify issues such as theft, loss, or mismanagement.
What Is Safety Stock and Why Is It Important?
Safety stock is extra inventory held to guard against uncertainties in demand and supply. It acts as a buffer to prevent stockouts and ensure that products are available for customers, helping to maintain service levels and customer satisfaction.
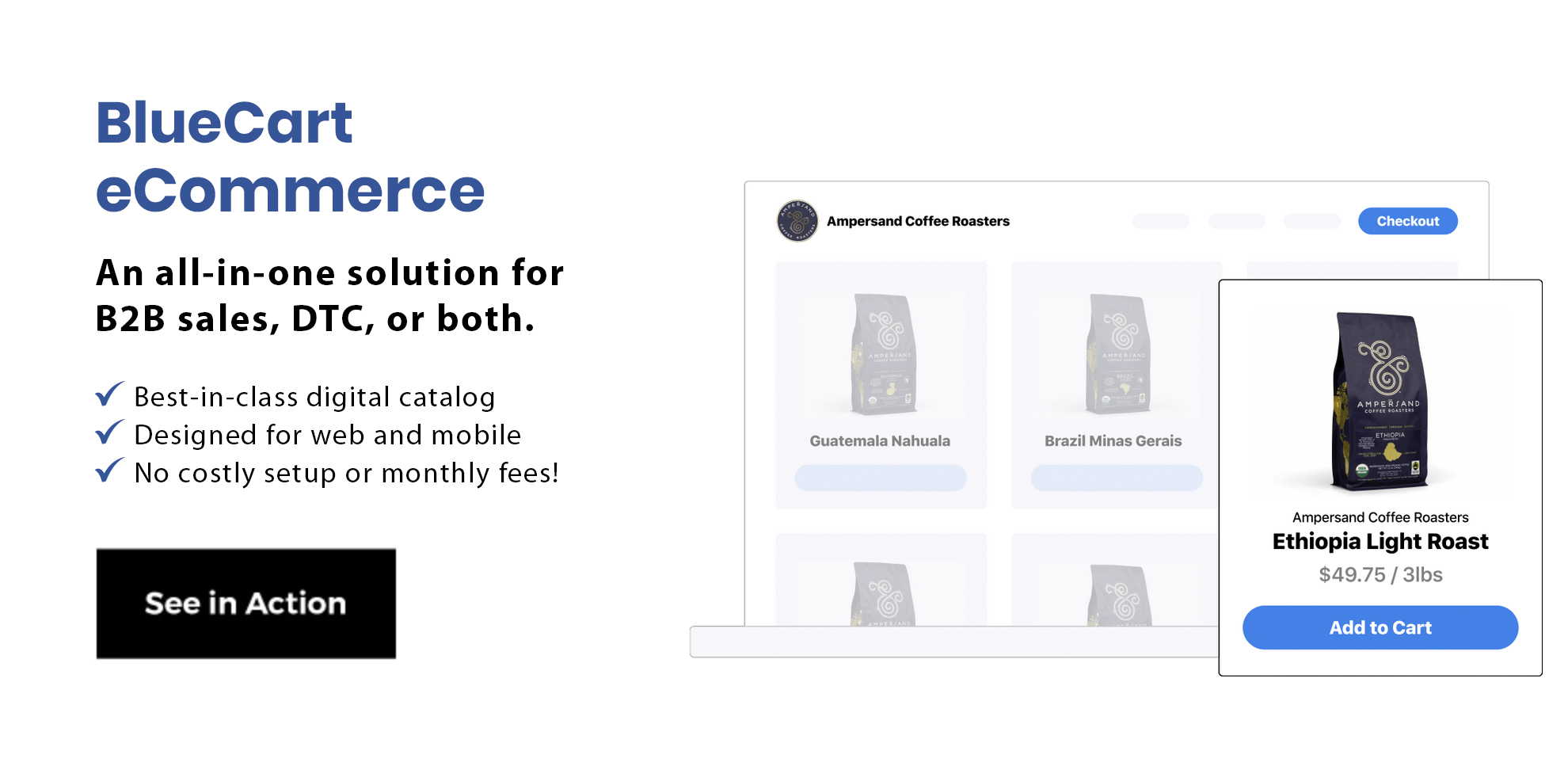
Inventory Definition: That’s Definitely a Full Inventory!
Thus ends our exploration of what is inventory and the definition of inventory. There are a lot of related concepts and definitions. A solid grasp of them provides good context for a deeper understanding of what inventory means.
And what makes us qualified to provide such a definition?
We created an industry-leading B2B eCommerce platform and online marketplace that helps businesses manage their inventories smoothly.